
GIE Media

1) What applications benefit from large horizontal machining? The VHP160 XP machine design is a radical departure from any other current design. Its “fully closed, force-loop construction” was developed specifically for machining monolithic aerospace components. This was only achieved after more than six years of working closely with several large manufacturers of these types of parts.
2) How does this large machine maintain accuracy? Maintaining accuracy on a machine this size starts with the initial design. The thermally symmetrical construction of the base, table, and column that houses the machine spindle helps to ensure consistent, high-accuracy machining throughout
3) What are the advantages to horizontal indexing? Being able to load and unload the parts with the table in the horizontal position allows gravity to work in our favor and reduce the time required for this operation. In many cases, part location and fixturing are simpler. However, for actual machining, chip and coolant control are far better when the part is in a vertical plane. With the part in this attitude and the use of the available high-volume coolant, chips are flushed out of the workpiece as they are produced, ensuring a better part finish.

4) How much customization is possible? For the U.S. market, this machine is offered in two basic models – the VHP160 with a 120hp spindle and 1,250mm x 4,000mm table, and the VHP160 XP which comes with a 160hp spindle and 1,400mm x 4,000mm table. Either machine is available with a single-table or with a two-table changer and 60 to 120 tools (or more with customization). They may be configured into multiple machine cells incorporating a table transporter vehicle, table stockers that allow tables to be stored either vertically or horizontally, and multiple

5) What should a shop consider before committing to such a large machine? Purchasing this type of machine is a big commitment. Since the design of the machine is for a very specific family of parts, it is not to be confused with the typical large-envelope, job-shop machine. Parts produced on this machine must meet the highest standards for quality control and surface finish. A potential customer needs to ensure space is available for the machine and material, tooling, and balancing equipment capable of supporting the 30,000rpm spindle – and most importantly, the ability to secure the contracts to keep work on the machine.
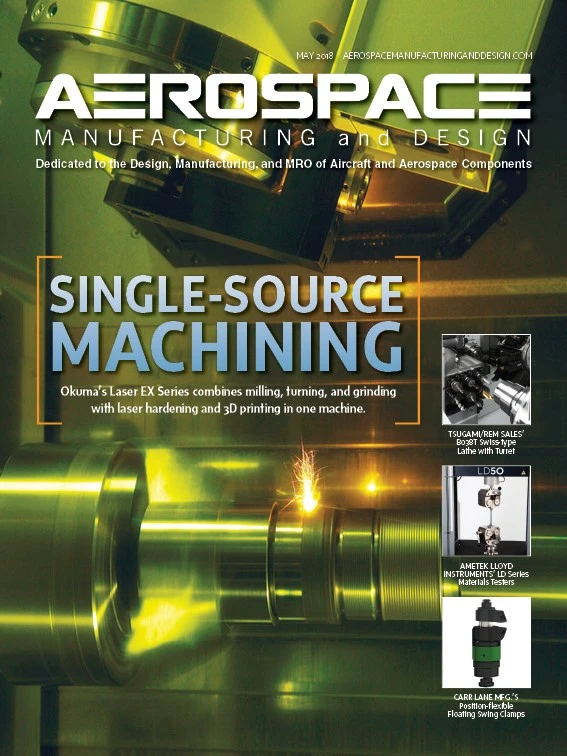
Explore the May 2018 Issue
Check out more from this issue and find your next story to read.
Latest from Aerospace Manufacturing and Design
- Cyient Group, Deutsche Aircraft finalize multi-year contract
- High surface quality at high speed
- #57 - Manufacturing Matters - Agile & Robust Supply Chain Management with Lisa Anderson
- Take control of your manufacturing business despite supply chain turmoil
- Strengthening the defense maritime industrial base for national security, economic resilience
- Register now to learn solutions for high-temperature aerospace machining challenges
- Expertise on machining, joining offered in April’s Manufacturing Lunch + Learn
- NASA offers free high school engineering program this summer