
GIE Media

A hole is one of the most common features in typical aerospace components, providing clearance, location, connection, or weight reduction in parts and assemblies. Geometric dimensioning and tolerancing (GD&T) requirements can create unique challenges when drilling a wide range of material types that require different machining methods.
1) What are the greatest challenges in drilling for the aerospace manufacturing market? Quality standards are critical in aerospace parts. Hole position, size, roundness, straightness, and finish requirements are usually tight. To create proper holes, you need drilling tools engineered to meet these requirements. ISCAR provides self-centering geometries (HCP, HFP, and QCP-2M) in the SumoCham line to help with true position. This eliminates the spot drill or center-drilling process. SumoCham family drills are available from 4mm (0.157") to 25.9mm (1.295") in 0.1mm (0.004") increments. A similar tool, ChamIQ 700, covers 26mm (1.299") to 40mm (1.575") in 0.5mm (0.020") increments. Several common imperial sizes are also available. Drill bodies come in standard lengths of 1.5xD, 3xD, 5xD, 8xD, and 12xD.
2) What typical materials are encountered, and do they create any problems? Aerospace materials vary from aluminum, alloy steels, 300 series and PH stainless, titanium, Inconel, or Hastelloy. This wide variety of materials requires various edge preps – sharp, honed, T-land, or polished. Carrying inventory of all these types in solid carbide drills can be expensive. Indexable head drills become more economical, allowing shops to cut various materials from one drill body that accepts several types of carbide heads.
3) What setup aspects are critical to drilling quality holes? Drilling precise holes requires precise tool holders. Total indicator runout (TIR) is critical to produce quality holes. Manufacturers now offer runout compensation tooling, such as the ISCAR FineFit collet chuck that allows a tool to be dialed in to a TIR of 0.0008" or less. This is even more critical in reaming operations with carbide heads running at high speeds, such as ISCAR’s Bayo-T-Ream.
4) Continuous cutting is common, but how do you handle interrupted cuts such as cross holes? Double margin geometry heads (ICP-2M, QCP-2M) provide additional stability in interrupted cuts such as cross holes or angular entry and/or exit. It is important to reduce feed rates 30% to 50% through the interruptions. ISCAR introduced a new product, LogIQ3Cham with three flutes. This configuration provides additional improved stability for discontinuous cutting.

5) What processes are used for finishing? Reaming or boring is used to control diameter, roundness cylindricity, and straightness. Often, these secondary operations can be eliminated since IT8-IT9 hole tolerance is possible with SumoCham. Also, double-margin and wiper geometries can help improve finish, straightness, and roundness. Another finish operation is threading. With 0.1mm steps, a pre-hole can be expanded up or down in small increments to change the percentage of thread form for tapping or thread milling.
For more info: http://www.iscarusa.com
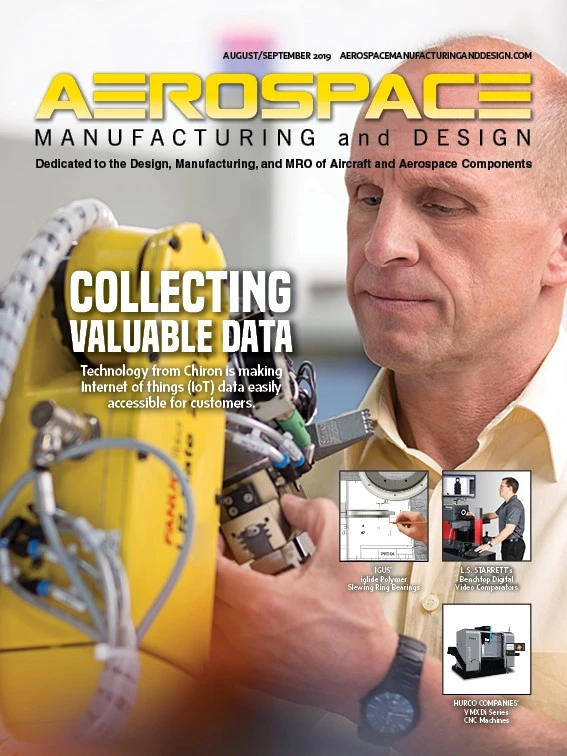
Explore the August September 2019 Issue
Check out more from this issue and find your next story to read.
Latest from Aerospace Manufacturing and Design
- Heart Aerospace relocates to Los Angeles
- Fixtureworks introduces Stablelock Clamps
- Piasecki acquires Kaman's KARGO UAV program
- PI Americas’ long-travel XY piezo nanopositioners-scanners
- AAMI project call submission deadline extended to May 12
- Jergens launches cast iron tooling column additions
- Airbus to acquire assets relating to its aircraft production from Spirit AeroSystems
- FANUC America's Cobot and Go web tool