
1) What differentiates Greenleaf’s standard and custom indexable tooling solutions?
When responding to customer needs, Greenleaf is focused on providing speed. We have partnerships with key customers within the aerospace industry.
Standard applications are processed directly through our Customer Service department. For custom applications, Greenleaf targets 48 hours for description quotes, 72 hours for a full quote of individual tools, and five days for a complete tooling layout of aerospace components. Greenleaf provides this level of service by identifying application requirements, ensuring the request is routed and processed through our quotation system accurately and quickly.
2) What is Greenleaf’s philosophy for working with aerospace clients?
Greenleaf has always focused on understanding the needs of the aerospace industry and is committed to being a value-added partner. Practically every machined metal part on an aircraft has been touched by a Greenleaf product.
We leverage this background, along with the knowledge and experience of our Engineering team and our high-volume manufacturing facility, when working on new projects. The key to our success is flexibility. Greenleaf runs toward challenging applications that others avoid.

3) What disruptive technology is Greenleaf pioneering to benefit aerospace engine part manufacturers?
Greenleaf has developed an indexable milling solution to slot mill turbine discs and blisks. Traditionally, these parts have been broached or milled with a solid carbide end mill, both of which are very time consuming and expensive.
Our indexable slotting tools, both straight and curved, can use carbide or ceramic inserts, and we have reduced the time it takes to mill a slot/vane on a blisk from an average of 30 minutes down to three minutes! This 10x increase in productivity dramatically increases throughput. Plus, an indexable insert solution is much more economical and avoids regrinding solid-carbide end mills or large, high-speed broaches. Greenleaf’s indexable slotting tools are simpler and much more cost effective.
4) What other areas benefit from Greenleaf’s ceramic tooling expertise and technology?
From roughing with scale to finishing, Greenleaf has the right products to deliver productivity and results. Although some think that finishing is for carbide only, Greenleaf has proven successfully that you can finish with ceramics. We highly recommend using our ceramic grade WG-600® with a T1 edge prep for increased strength and minimum smearing during finishing operations. When roughing scale cuts, we recommend using the strongest insert shape possible (a round insert or the largest corner radius possible) in our ceramic grade XSYTIN®-1. A T2A edge prep works best for roughing and other heavy- duty machining applications.
5) What makes Greenleaf unique in the tooling industry?
Greenleaf was founded on a spirit of innovation and technology nearly 75 years ago. With the recent introduction of our XSYTIN®-1 phase-toughened ceramic grade, to our proprietary solution for indexable milling of turbine discs and blisks, we continue to reach new heights of productive tooling solutions.
We typically see productivity increases of 10x when we convert aerospace customers to using a Greenleaf product. That performance gain is only possible by having breakthrough materials technology, the absolute best quality, and highly skilled applications engineers who can properly apply the product. Speed, flexibility, innovation, quality, and great people are a tough combination to beat!
For more info: http://www.greenleafcorporation.com
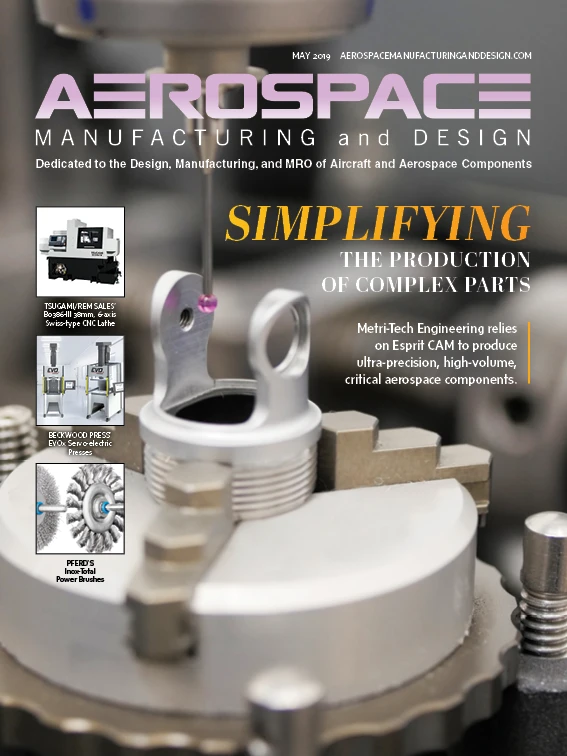
Explore the May 2019 Issue
Check out more from this issue and find your next story to read.
Latest from Aerospace Manufacturing and Design
- Ralliant to establish global headquarters in North Carolina
- Philatron MIL-DTL-3432 military cables
- Beyond Aero refines its hydrogen-electric light jet
- Americase's advanced protective solutions
- Social media - what are your thoughts
- GE Aerospace secures Air Force engine contract
- Thomson Industries' online sizing and selection tool
- #53 - Manufacturing Matters - 2024 Leaders in Manufacturing Roundtable