
The profitability of working on heat-resistant
Thanks to technological advances, from the machine tool down to the cutting tool, more machining operations can benefit despite the challenging nature of aerospace work.

1) What are the most common aerospace machining challenges?
BV: The geometric nature of aerospace parts makes them among the most difficult to machine due to variables such as temperature, tool life, chip evacuation, part access, and machine maintenance.
Add to that pressure to deliver products faster, at a lower cost and in small lot sizes, and more manufacturers are searching for ways to make processes more efficient.
2) How are machine tool manufacturers addressing the challenge of cutting difficult shapes?
BV: Cutting curves with straight tools is difficult. The advent of simultaneous part and spindle movement, and swivel and linear axis combinations makes it much easier; swivel ranges up to 225° in the A-axis and 360° in the B-axis, along with retractable (tunnel) spindles, allow for full access to the work area, the entire length of the tool, and every non-fixture feature of the part. Workholding offerings have advanced, too, namely bridges, reductions, extensions, and even chucks that can pivot.

3) How can machine shops increase production for small lot sizes?
BV: In high-mix, low-volume manufacturing, efficiency in
Space-efficient tooling magazines can be integrated into machinery in a variety of configurations as
Since the table of the G550T can rotate up to 800rpm, some machining steps can be executed as turning operations in addition to milling.
4) How do you control heat buildup on the cutter or part that can lead to scrapping expensive material?

BV: Overhead machining – flipping the part upside down – takes advantage of gravity to remove chips.
The latest cutting tool geometries and coatings allow cutters to retain the sharp edges needed to shear the strongest materials, forming chips that absorb heat, flow cleanly up flutes, and leave the cut without consequence.
Chip disposal by a scraper-type conveyor at the base of the machine dissipates heat in the work area and keeps it from transferring into the machine’s structure.
5) Do these added features make machine maintenance more difficult?
BV: Maintenance of these machines is much easier than it once was, with easily accessed components and integrated chip removal and coolant systems. What’s more, tool cleaning devices loaded into the tool magazine can brush or air-clean conical and flat surfaces of the tool interface to fully enable unmanned machining.
Get curated news on YOUR industry.
Enter your email to receive our newsletters.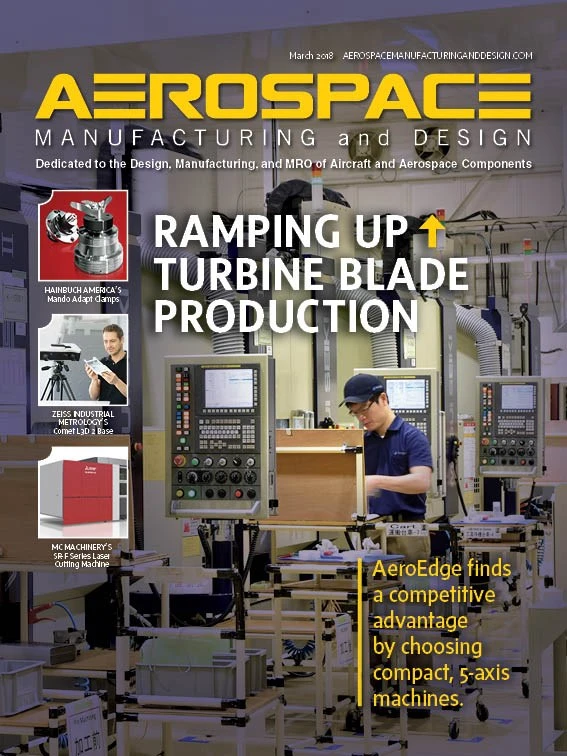
Explore the March 2018 Issue
Check out more from this issue and find your next story to read.
Latest from Aerospace Manufacturing and Design
- GE Aerospace secures Air Force engine contract
- Thomson Industries' online sizing and selection tool
- #53 - Manufacturing Matters - 2024 Leaders in Manufacturing Roundtable
- Join us for insights on one of the hottest topics in manufacturing!
- You can still register for March’s Manufacturing Lunch + Learn!
- Ohio creates Youngstown Innovation Hub for Aerospace and Defense
- Tormach’s Chip Conveyor Kit for the 1500MX CNC Mill
- How to Reduce First Article Inspection Creation Time by 70% to 90% with DISCUS Software