
GIE Media

1) What does Greenleaf offer aerospace parts manufacturers?
We’ve all heard the sayings time is our most precious commodity and time is money! That couldn’t be truer than in aerospace parts manufacturing where machining hourly rates are high, the materials are exotic and difficult-to-machine, and the quality requirements are strict. This creates a tremendous opportunity to add value through great, high-performance tooling solutions, technical applications support, and outstanding customer service. Greenleaf is the world leader in high-performance ceramic tooling and technical ceramics, so we know the ins and outs of saving time and money.
2) What performance advantages are possible?
We like to keep things simple for our customers. When ceramics are applicable, we will make a commitment to do the same job in much less time, equaling more profit for our customers. In most cases, we can reduce overall machining time by 6x to 10x, a value proposition that’s tough to beat. Getting more parts across the machine and out the door faster will free up machining time to manufacture other products or take on more volume.
3) What are the right applications for ceramics?
Ceramic tooling is applicable to a broad range of workpiece materials including nickel- and cobalt-based alloys, hardened materials, select stainless steels, cast and ductile irons, and materials with heavy interruptions and scale. Once the workpiece material is deemed a good fit for ceramics, we need to be sure the machine has a good, solid spindle capable of the required speeds. You also need good fixturing for the workpiece to avoid vibration and harmonics, which are detrimental to ceramic machining.
4) How do you know when to choose ceramic, carbide, or CBN?
As we’ve seen advancement in ceramic material science, we are expanding the field of operation where ceramics can be applied. We’ve successfully machined medium carbon steels with XSYTIN®-1, our newest ceramic, at 1,600sfm compared to 1,000sfm with carbide. XSYTIN®-1 also works well in heavy, interrupted cuts and cutting through the nasty scale of forgings or heat-treated materials.
I continue to be amazed at what XSYTIN®-1 will cut. Every day we find opportunities to convert customers to ceramics. When hard turning shafts with ceramics, we successfully replace CBN inserts and offer greater value.

5) What sets Greenleaf apart from other cutting tool manufacturers?
Greenleaf prides itself on running toward opportunities that others walk away from. Our custom-engineered tooling solutions offer unique features and capabilities that allow customers to process their parts in the most efficient manner possible. We start by looking at the entire process and understanding what the customer wants to achieve. Once we know the goal, we assess the machine, fixture, part, material, and coolant needs to make sure we develop the best custom-engineered solution available. Greenleaf has more than 150 years of design engineering expertise, and we have developed more than 125,000 unique custom tooling solutions for our customers.
Custom steel and insert tooling is a core part of what we do for our customers. When you wrap innovative technology, custom engineering, superior customer service, and on-time delivery into one package, customers keep coming back for more. We like that!
For more info: http://www.greenleafcorporation.com
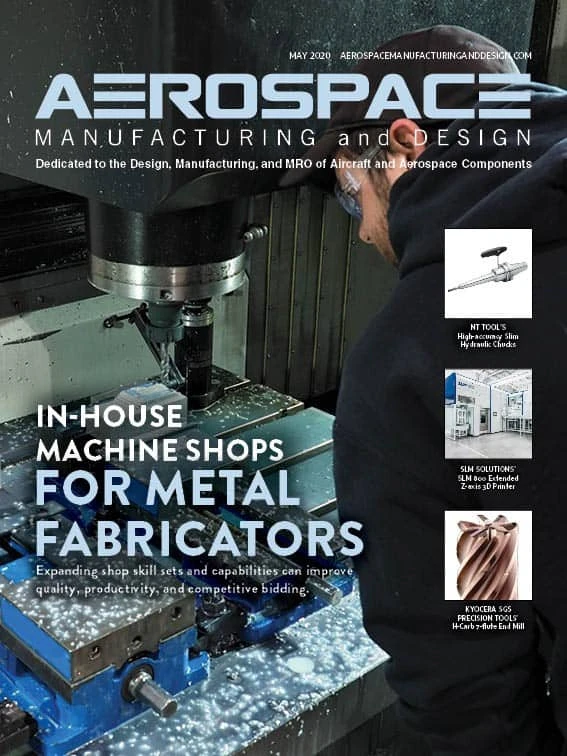
Explore the May 2020 Issue
Check out more from this issue and find your next story to read.
Latest from Aerospace Manufacturing and Design
- BOC Aviation orders 120 Airbus, Boeing jetliners
- Mazak’s INTEGREX j-Series NEO
- Embraer tests wing for new technologies demonstrator
- Mitutoyo America’s SJ-220 portable surface roughness tester
- #55 - Manufacturing Matters - A Primer on Defense Contract Manufacturing
- Registration is open for April’s Manufacturing Lunch + Learn!
- Natilus begins search for new home to build world's most efficient commercial aircraft
- Aerospace Industry Outlook webinar is back by popular demand