
Manufacturers using plasma, laser, and waterjet cutting machines are all looking for next-generation performance. New or upgraded machine purchases should provide capabilities that allow faster, more reliable production of higher-quality products. The reputation and success of a machine builder depends on demonstrating the best performance, design, and integration.
Optimizing the motion system improves all three. Five key opportunities for improvement include the fieldbus architecture, control loop bandwidth, servo motor design, feedback selection, and cabling.
Choose the right fieldbus architecture
Modern material forming systems almost universally employ some version of Ethernet for ease of use and performance. But within the Ethernet family, performance is relative, and choosing the wrong bus architecture can significantly reduce the execution speed, degrading cut quality and precision.
Whether using an industry-standard controller such as Hypertherm or a custom controller, the position points that define the cut are streamed from the controller to the drive deterministically. The time intervals between each X/Y set of points are strict and undeviating. Additionally, for highly dynamic applications such as precision cutting, these time intervals are very short – typically within the 500 microseconds to 1 millisecond range. Longer time intervals mean a less precise cut, while varying time intervals mean a distorted cut.
Ethernet connectors look the same, but various versions behave differently, so it’s essential to choose the right option (see Table 1, bottom left). Any drive’s fieldbus ports, however, must support a version of industrial Ethernet, and all devices on the bus must be compatible and correctly configured.
At Kollmorgen, we recommend EtherCAT for its fast, real-time performance as well as its support for CANopen, FailSafe over EtherCAT (FSoE), and other characteristics.
Optimize bandwidth
Higher bandwidth is intrinsically related to higher speed. Increasing control loop bandwidth stiffens motor behavior, decreases error, and improves transient response times. The result is more responsive control of position, velocity, and torque. For many everyday cutting applications, these factors may not be critical, but for next-generation cutting machines, control loop bandwidth is essential to performance.
However, while high bandwidth enables high performance, it also requires high-performing motion components. Higher frequencies might cause instability if the drive and motor aren’t able to take advantage of the rapid changes in the control loops. For example, a motor with high inertia may not achieve the required acceleration, and those limitations feed back into the control loops.
Another common issue is bandwidth-matching. A multi-axis application needs sufficient bandwidth to perform the required moves on each axis. But if the bandwidth doesn’t exactly match the different axes, the axes could respond at different rates to the control loop feedback, distorting the cut’s shape. While not directly related to bandwidth, applications incorporating a gantry also need cross-coupling between the axes on the two parallel sides to ensure coordinated motion.
Drives should provide simple, highly accurate tools for matching bandwidth across axes. When deciding on a servo motor, look for low-inertia designs to provide the acceleration and torque response needed in high-bandwidth, high-performance applications without creating disturbances in the system.

Select, size motors appropriately
Another common mistake is undersizing a motor or selecting the wrong motor design without considering the risk of voltage or current saturation. A motor’s torque constant (Kt) can’t be higher than what the bus voltage will allow. If the drive can’t supply the necessary voltage or current, you may not be able to get the motor to perform required movements.
Incorporating electrical calculations up-front as part of the motor selection process prevents these problems. With a precise understanding of the available current and voltage, you can objectively evaluate the motor design and size needed.

You may need to move to a bigger motor. Alternatively, you can consider the same motor with a different winding that balances voltage and current requirements. It’s highly probable you can get the performance needed without upsizing the motor or gain the ability to downsize.
Partners with motion engineering and product selection expertise can eliminate voltage and current saturation problems and ensure optimum performance given the realities of your electrical supply.
Match feedback devices to application requirements
Feedback devices provide information to the drive or controller to ensure that the motor or load reaches the required speed and position at the right time. Such devices can significantly influence cost, speed, and accuracy.
Incremental encoders provide two output signals indicating movement and direction, tracking only relative position, so users need digital interfaces to calculate absolute position. During a power interruption or application failure, the axis must be returned to a home position before restarting since the encoder doesn’t track absolute position. In some applications, this can be a safety issue. Incremental encoders are also somewhat susceptible to electrical noise interference and may require input filters and other measures to ameliorate the problem.
Absolute encoders generally cost more than incremental ones but provide several advantages. They generate digital codes representing the motor shaft angle, providing exact position and speed information without requiring further processing. If power is interrupted, an absolute encoder reports the correct position upon restart without needing to return to a home position. These encoders are also capable of very high resolution, provide excellent noise immunity, and are available in single-cable options.
Resolvers are another option. These analog devices are designed around an electrical transformer, using voltage comparisons between rotor and stator windings to provide absolute position throughout a turn of the motor shaft. Resolvers are rugged devices often specified for use in harsh environments, but typically don’t provide the resolution needed for high-precision cutting.

Each feedback type has its own use, but it’s essential to choose the most appropriate technology for the machine performance desired. Be aware that inexpensive feedback devices have hidden costs, such as difficulties in tuning motion to reliably meet requirements.

Choose cables for reliability, performance
It’s easy to overlook the importance of cables, but this isn’t an area to scrimp or treat as an afterthought. Undersized wire gauges in the cable will create problems with efficiency and reliability. If cables aren’t properly grounded and shielded, electrical noise can cause feedback errors and reduce system performance. Substandard insulation and connectors can cause failures throughout long-term use.
The cable number, size, weight, flexibility, and layout can also make a difference. In a gantry system, cables are part of the load, causing drag, weight, and compliance issues that the servo system must compensate for. A single-cable design may be useful because the cable and connector are easier to route and lighter than a two-cable system.
A gantry driven by a larger motor may benefit from the flexibility of two cables instead of a thick, stiff, single cable. As with all aspects of machine design, cable selection requires balancing properties without compromising quality.
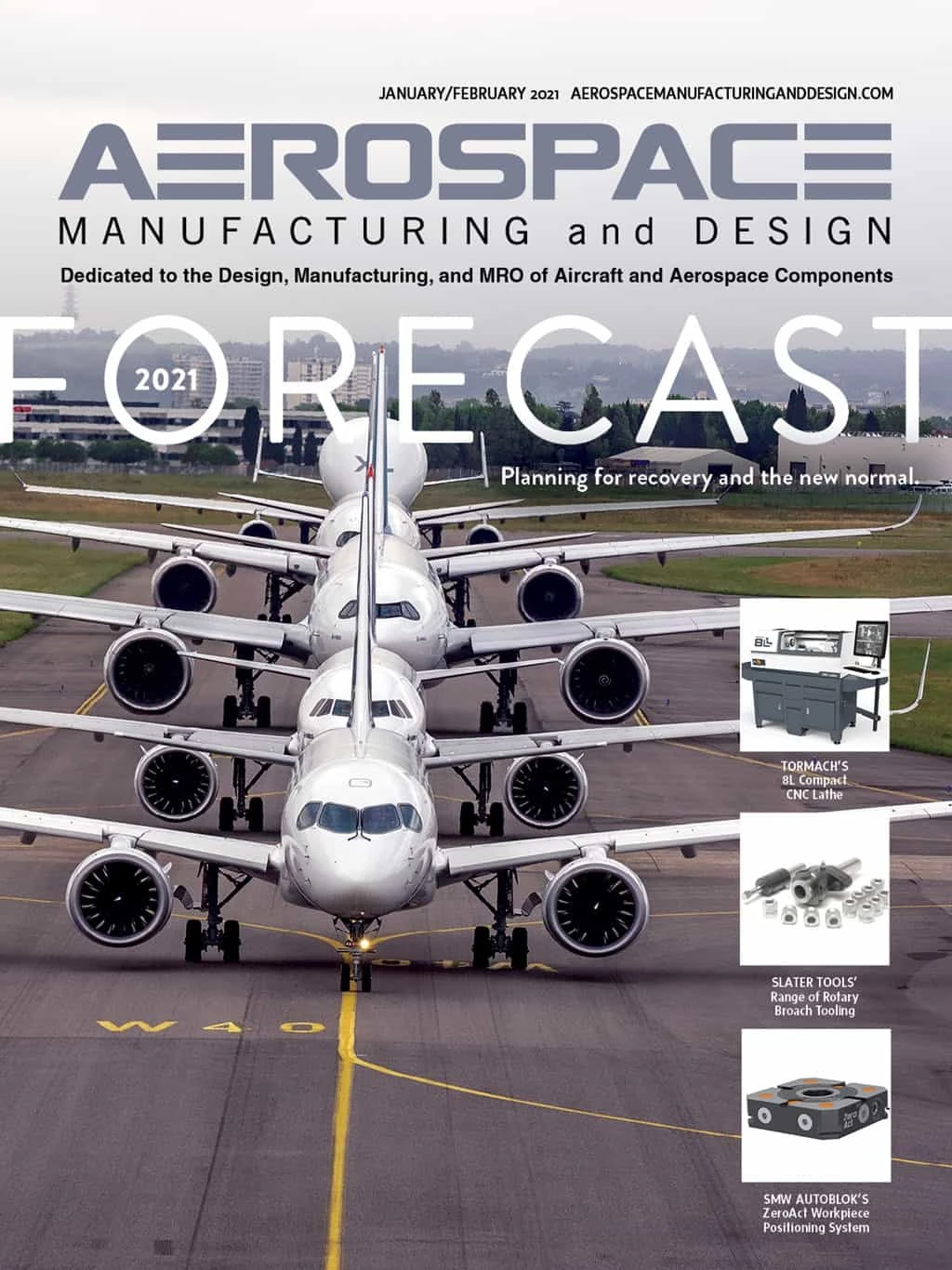
Explore the January February 2021 Issue
Check out more from this issue and find your next story to read.
Latest from Aerospace Manufacturing and Design
- Piasecki acquires Kaman's KARGO UAV program
- PI Americas’ long-travel XY piezo nanopositioners-scanners
- AAMI project call submission deadline extended to May 12
- Jergens launches cast iron tooling column additions
- Airbus to acquire assets relating to its aircraft production from Spirit AeroSystems
- FANUC America's Cobot and Go web tool
- Chicago Innovation Days 2025: Shaping the future of manufacturing
- High-density DC/DC converters for mission-critical applications