
STC-MTV 5-axis mill-turn machining centers excel in hard metal machining for aerospace engine casings and gearboxes, offering single setup milling, boring, drilling, tapping, and turning of Ti6AL4V and Ti5553 titanium alloys, nickel-based super alloys, and high alloy steels, producing superior surface finishes on complex and thin-wall parts.
A geared A-axis spindle drive with compact 1D-head allows use of short tools and large bearings for high metal removal rates. The steel worm wheel boasts high stiffness and excellent damping due to a specially coated damping disk in the 1D-head. A Siemens 840D controls heavy roughing, semi-finishing, and finishing.
Integrated 200 bar/3,000psi high-pressure coolant permits one-hit turning, and the machines’ 30hp angular automatic milling head enables easy access to internal surfaces and features. The angle head is loaded automatically from the tool magazine and tools in the head can be changed automatically.


Adaptive tool monitoring system
The updated tool monitoring adaptive control (TMAC) system version 3.0 performs real-time detection and uses high-precision, multi-range sensors to determine if a tool is worn or broken. TMAC has a high-speed processor that collects data 200x/sec and directly interfaces with any CNC control to react instantly to wear and extreme conditions.
TMAC 3.0’s streamlined user interface offers numerous configurations for viewing tool and sensor data. The processor houses its own web server, making the human-machine interface (HMI) browser-based and enabling real-time monitoring from a network connected device. Users with assigned permissions have live access to all TMAC systems on a shop floor from a single browser.
An adaptive control mode optimizes cutting with conditions changing due to wear, variations in material hardness, consistency, and depth of cut. Using a power sensor, TMAC overrides the machine tool feed rate to maintain constant spindle motor power during cutting, which increases productivity, extends tool life, and reduces cycle time up to 60%.
TMAC also monitors sensors for vibration, strain, coolant pressure and flow, and spindle speed. Users can customize views to show up to 4 sensor channels simultaneously in a single view.
Fixed abrasive buffing wheels
Fixed Abrasive Buff (FAB) buffing wheels can reduce the need for buffing compounds. Abrasive grains incorporated into the buffing wheel consistently produce 1Ra to 5Ra surface values.
The tear resistant, waterproof, durable wheels offer longer life than traditional cotton buffs. Premium silicon carbide abrasive, uniformly dispersed and applied to both sides of the cloth, results in more consistent buffing, generating more parts per buff with fewer wheel changes. The wheels can be added into new or existing robotic buffing applications.
By decreasing the need for buffing compound, the wheels offer a more efficient, cleaner, and safer way of buffing that minimizes costs, reducing cumbersome, time consuming clean-up in buffing operations and post-clean-up processes. Also, less buffing compound improves worksite safety and reduces the environmental impact of compound disposal.
Key applications for FAB wheels include automatic or semi-automatic buffing, cut buffing, and mush buffing. The wheels are effective on hard alloys as well as soft metals such as aluminum and brass. They are available in 5" to 22" OD, in 12- or 16-ply, 2- or 4-pack (waviness of the buff face), and various ID hole designs.
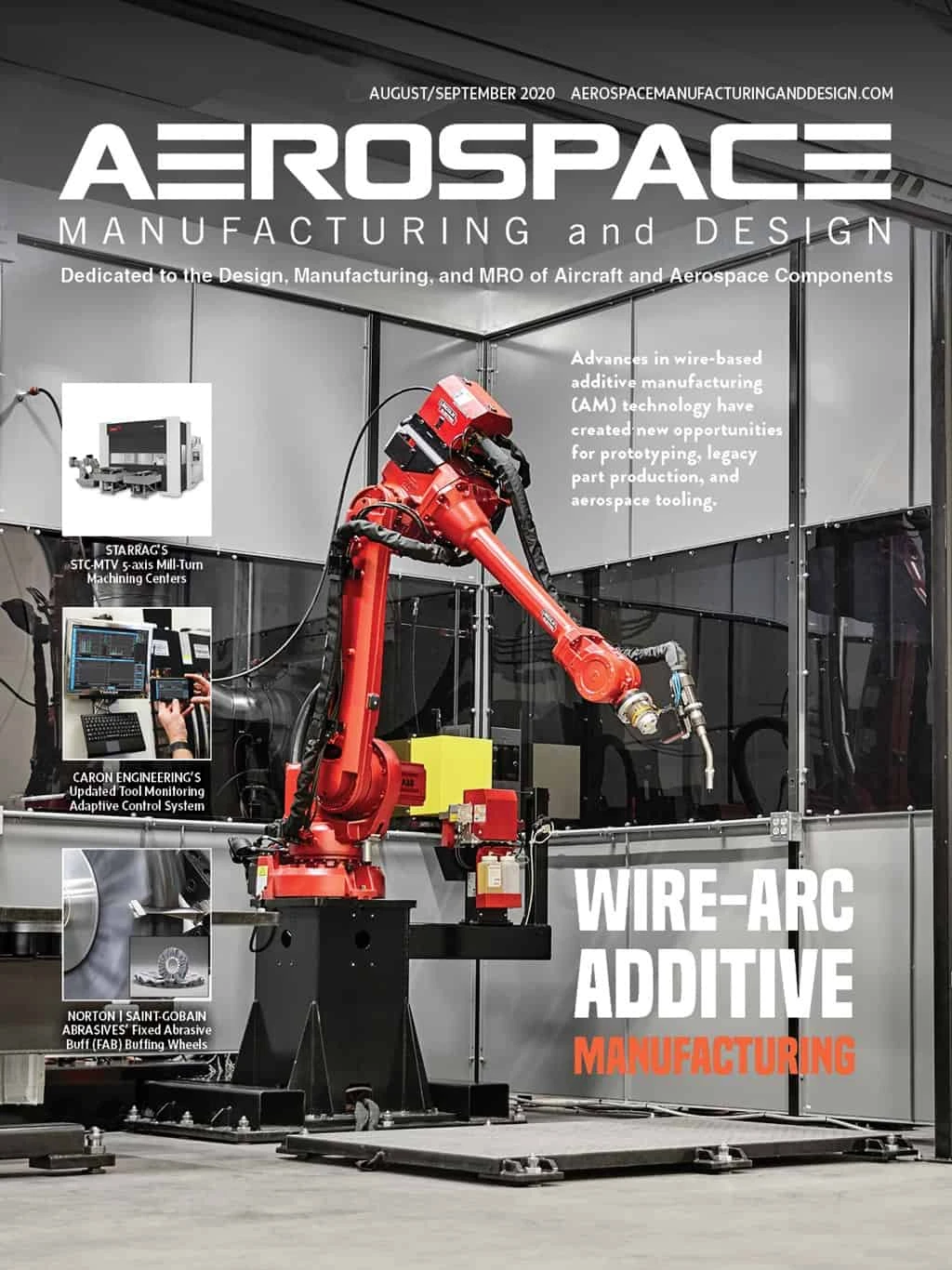
Explore the August September 2020 Issue
Check out more from this issue and find your next story to read.
Latest from Aerospace Manufacturing and Design
- Revitalizing the Defense Maritime Industrial Base with Blue Forge Alliance
- Safran Defense & Space opens US defense HQ
- Two miniature absolute encoders join US Digital’s lineup
- Lockheed Martin completes Orion for Artemis II
- Cylinder CMMs for complex symmetrical workpieces
- University of Oklahoma research fuels UAS development
- Motorized vision measuring system
- Everyone's talking tariffs