
Manufacturers could slash 90% off finishing cycle times when machining deep-pocketed workpieces. This can be achieved by combining 5-axis tangent machining with conical barrel cutters. Additionally, tangential plane machining can produce excellent surface quality and longer tool life.
Aerospace Manufacturing and Design was given exclusive access to a recent seminar demonstrating this machining strategy for aerospace applications at Grob Systems in Bluffton, Ohio.
To showcase the new method, a Grob Systems G350, 5-axis horizontal machining center (HMC) used Open Mind Technologies’ hyperMILL computer-aided manufacturing (CAM) software – which enables the technique – and Emuge cutting tools adapted for the purpose.
Peter Brambs, Open Mind Technologies’ director of product innovation, explains the 5-axis machining strategy and use of conical barrel cutters. Since the barrel cutter features radii from 250mm to 1,500mm, it can be used for large step-overs. The
Five-axis machining makes it possible to cut challenging geometries, free-form surfaces, and deep cavities more efficiently, Brambs says. The CAM system generates tool paths automatically with automatic collision checking and avoidance.

The machine
The Grob G350 is compact, rigid, and offers many spindle and table configurations. The 5-axis model, with A/B table, enables single setup machining of five sides; complex, 5-axis simultaneous 3D surfaces; and multi-angled holes, forms, and profiles.
To work with the software, the machine includes acceleration-dependent, feed-forward control; a load-sensitive drive control; an optimized spindle design, drive unit,
The machine complements the CAM system by allowing linearized tool paths and the ability to reach programmed speeds faster with greater accuracy. While some large machines are fast only on straight lines, smaller machines can be more agile, optimizing the software’s performance.
Rapid machine movements also reduce the time spent not cutting, notes Stefan Moessmer, a Grob aerospace specialist.
The G350’s slim spindle and symmetrical milling head
G350 HORIZONTAL MILLING MACHINE

The 31.69" Z-axis stroke and three roller guide carriages for each guideway maximize stiffness. The tool axis (Z) damping performance is supported by having the motorized spindle guided along the Z- and X-axis, reducing vibration on tooling and the machining center.
The 15.7" square table offers space for 5-axis machining, with part access enhanced by the A-axis tilting range of 225°.
The software
Open Mind’s hyperMILL MAXX Machining performance package has modules for roughing, finishing, and drilling. It also enables the 5-axis tangent-plane machining strategy.
Roughing includes cycles for trochoidal tool path milling for high-performance cutting (HPC) of prismatic and curved component faces. Dynamic feed rate adjusts according to cutting conditions for maximum material removal, and algorithms remove a constant chip volume to reduce tool stresses and increase roughing speeds 20% to 70%.
The finishing module includes pre-finishing and finishing of planes and free-form surfaces with various barrel cutters. The surface finish depends on the step-over distance and barrel radius. The quality of a workpiece surface decreases as the line increment increases and improves as the tool diameter gets larger. Since the tool shank diameter can only be increased within the limits of the machine tool, barrel cutters only work with a section of the desired tool diameter – a circle segment. Larger step-over distances can be realized due to the bigger radius to achieve
Managing director of Open Mind Technologies Alan Levine notes the hyperMILL MAXX Machining finishing process has been extended to other geometric shapes, such as ruled, curved surfaces.
Conical barrel cutters can machine geometry that is either too tall for efficient swarf milling or too tall for fast cutting with ball mills, such as aero-engine
In 5-axis helical drilling, holes can be machined with a forward lead angle. Tilting the angle to the side helps avoid collisions. For planes that do not need to be machined simultaneously or on large machine tools, the finishing module can also produce tool paths for 3+2 indexed machining. Only one tool is needed for different drill diameters, pre-drilling is not necessary, and the strategy supports hard-to-cut materials.
The programming process is easy by only selecting planar surfaces and having the system automatically detect boundaries, edges, and other features. Existing customers have implemented this new technique within an hour, Levine says.
The tooling
Traditional ball-nose end mills can prevent the tool from fully accessing features on workpieces. With a conical barrel cutter, the radius is ground along a cone angle relative to the cutter axis, offering better accessibility into deep pockets. Conical barrel cutters also reduce step-overs and the need to polish planar surfaces.
Conical barrel cutters have a larger radius, which has been increased from 250mm to 1,500mm.
Path distances of 6mm and 8mm are possible, producing optimal surfaces and longer tool life. Conical barrel cutters can be applied to generalized surfaces found in landing gear, engine casings, and engine
Open Mind’s Levine points out that using standardized programming applications together with conical barrel cutters offers benefits including:
- The large radius that can be ground on a conical barrel cutter is greater than on a standard end mill
- Shorter cutters allow tool holders greater
access into the workpiece
Summary
With growing pressures in aerospace to reduce production times and increase efficiency, advanced manufacturing methods can help reach those goals. The development of innovative tool paths enables cutters to perform better and faster, and using a machine optimized for the task can reduce machining times and increase tool life. These advantages offer manufacturers a better way to compete for aerospace business.
Emuge Corp.
www.emuge.com
Grob Systems Inc.
www.grobgroup.com
Open Mind Technologies USA Inc.
www.openmind-tech.com
About the author: Eric Brothers is senior editor of AM&D and can be reached at 216.393.0228 or ebrothers@gie.net.
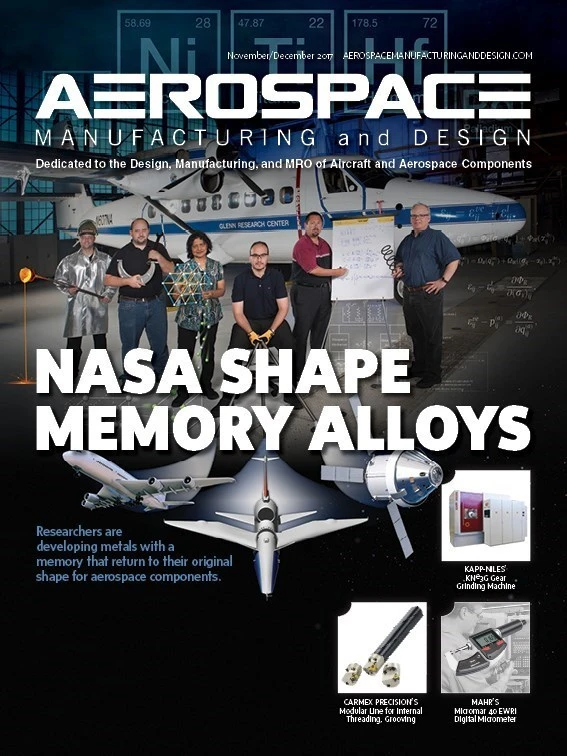
Explore the November December 2017 Issue
Check out more from this issue and find your next story to read.
Latest from Aerospace Manufacturing and Design
- NASA offers free high school engineering program this summer
- Pemamak's PEMA Vision 3D software
- Aerospace Industry Outlook - Spring 2025, presented by Richard Aboulafia
- Panama’s National Air and Naval Service selects Embraer Super Tucano
- Model 5770 Linear Abraser
- #42 Lunch + Learn Podcast - Quell Corp
- RECARO Aircraft Seating showcases advanced comfort solutions at AIX 2025
- Mitutoyo America’s MiSTAR 575 Shop Floor CNC CMM