
The 325linear 5-axis CNC grinder has extended X- and Y-axis movement, as well as two auxiliary slides for
On the A-axis, a user can install collet, hydraulic expansion, or multi-range chucks. The automated collet changer allows workpieces with different diameters to be clamped with high concentricity in an unmanned loader station. Position-oriented clamping of non-rotationally symmetrical workpieces supports presetting, so sequential workpieces with various roughing and finishing requirements can be continuously processed.
Schütte Integrated Grinding Software (SIGSpro) assigns clamping options for each grinding operation. Preset distances from the grinding wheel to the workpiece can be defined and held constant using the support and tool guidance system. In 3D mode, cycle steps can be simulated, controlled, and optimized for exact estimating, collision avoidance, and external workstation integration with other workpieces.
A 140-position tool changer, 5-24 grinding wheel magazine, and a flexible robotic tool gripper are available.
Schütte Corp.
http://www.schutteusa.com

Solid ceramic endmill
The SX9 solid ceramic endmill increases productivity in machining high temperature alloys. Its SiAlON ceramic’s durability and engineered flutes allow the endmill to achieve speeds up to 2,000sfm, more than 15x faster than standard carbide endmills. The 4-, 6-, and 8-flute endmill tools incorporate edge designs that resist chipping for longer tool life.
When machining Inconel 718 aerospace parts, the SX9 endmill completed a roughing and semi-finishing pass at 2,400sfm with superior results, reducing machine time to 4 minutes instead of the original tool’s 24 minutes.
NTK Cutting Tools USA
http://www.ntkcuttingtools.com

Zero-point clamping system
The Automatic Positioning System (APS) stationary
The APS locks into position by lining up a series of pins on the workpiece or
Heat-treated elements and a protective coating prevent rust, and the unit is sealed against dirt and swarf. Built-in air cleaning keeps the clamping system’s supporting surface free of chips during
SMW Autoblok Corp.
https://www.smwautoblok.com
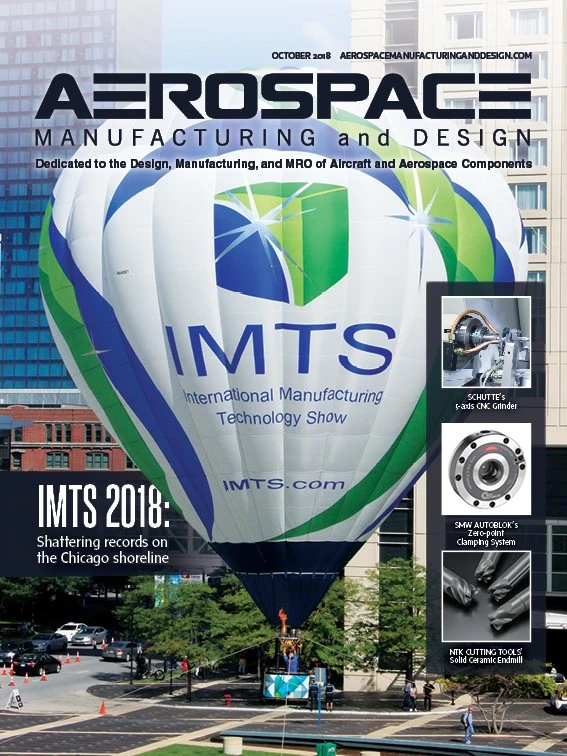
Explore the October 2018 Issue
Check out more from this issue and find your next story to read.
Latest from Aerospace Manufacturing and Design
- Strategies to improve milling and turning for medical components
- Being proactive about your business despite uncertainty
- Optimizing production of high-precision components through collaboration
- An inside look at the defense maritime industrial base
- Safran inaugurates advanced manufacturing and engineering hub
- Dillon pin location jaws
- NASA-supported technology outfits Venus Aerospace hypersonic engine
- To the Smoothest Surfaces, Finishes, and Beyond | Okuma GA26W