
The safety of an aircraft depends on the reliability of every component – from the smallest fastener to the largest subassembly. A single defect can have catastrophic consequences, showing just how critical it is to fix quality problems in aerospace and defense (A&D) manufacturing. Accenture research shows 83% of A&D executives say they still have quality concerns – costing the industry a whopping $80 billion each year in rework, scrap, and warranty repairs. But the real cost goes beyond just dollars and cents; it includes the intangible costs of damaged reputations, lost customer trust, legal expenses, and delayed innovations.
The root causes of quality issues in A&D are multifaceted. For one, the shortage of skilled engineers who understand warranty requirements, repair processes, and manufacturing is a major challenge. Cross-functional expertise – from structures to composites to hydraulics – is essential. Yet, the industry is grappling with high employee attrition rates and a skills gap hindering its ability to address quality issues effectively. Moreover, companies are early in their digital transformation journeys, with many still relying on manual and paper-based systems, leading to errors and delays. The lack of real-time data and automation makes it difficult to detect and rectify quality issues quickly.
To address these issues, companies must transform their quality programs. There are four main initiatives they can take to change the way they work, improve their systems, use automation, and create a system focused on quality:
1. Organizational renewal: More than just a culture change
Organizational renewal isn’t just about changing the way we think; it’s a strategic shift toward a skills-based approach. This means ensuring knowledge transfer from experienced staff to new hires and equipping the workforce with the skills needed to refine quality control processes. Technical skills are crucial, but soft skills such as communication, problem-solving, and adaptability are equally important for implementing resilient improvement strategies.
By investing in the right skills and fostering a culture of continuous improvement, organizations can better adapt to changing conditions and maintain high standards of quality. This includes regular training programs, mentorship initiatives, and a commitment to lifelong learning. A skilled and adaptable workforce is the foundation on which a quality-driven organization is built. New approaches using generative artificial intelligence (Gen AI) are being implemented that ensure faster and better-tailored upskilling for the top skills workers need to thrive. In an industry where safety is paramount, we can’t afford to skimp on training and development.
2. Quality control systems: The backbone of transformation
Quality control systems are the backbone of any quality transformation. Deploying advanced quality management systems (QMS) and integrating frameworks such as Advanced Product Quality Planning (APQP) with real-time data analytics and AI is essential for monitoring and improving quality at every stage of production. These systems enable proactive identification and resolution of issues, reducing the likelihood of defects and enhancing product reliability.
A QMS can automate and streamline quality processes, ensuring standardization, traceability, and compliance with industry regulations. Real-time data analytics and AI-driven insights can help predict and prevent non-conformances, ensuring quality issues are addressed before they become costly problems. By using these advanced systems, companies can achieve higher levels of precision and consistency in production processes.
A leading aerospace company implemented a QMS system, streamlining and automating quality processes to ensure standardization, traceability, and compliance with industry regulations. This reduced defects and improved overall product reliability and time to close nonconformances. The company’s investment in advanced QMS paid off, leading to significant improvements in operational efficiency and customer satisfaction. It’s a clear win and shows what’s possible when quality is prioritized.
3. Digital technology: Boosting precision and efficiency
Digital capabilities such as AI, operational technologies (OT), and advanced robotics can greatly improve production precision and efficiency. Automation reduces the need for manual intervention, minimizes errors, and allows for data- driven decision making. This can lead to a 20% reduction in lead times and a 30% increase in output, as demonstrated by a major aircraft manufacturer.
Robotic assembly, for example, improves build consistency and reduces non-conformances. Internet of Things (IoT) sensors can monitor products in real time, ensuring they remain within process tolerances. AI can analyze vast amounts of data to identify patterns and predict potential issues, enabling companies to take corrective actions before defects occur. These technologies boost productivity and reduce operational costs, making them essential for any quality-driven organization.
One defense manufacturer used IoT and AI to monitor key build characteristics in real time. By using statistical process control (SPC) with AI, the company made changes to increase time within process limits, improving quality and reducing costs. The use of real-time data analytics and AI-driven insights has enabled the company to maintain high standards of quality and reliability, even in the face of complex and dynamic production environments. It’s a testament to what can be achieved when we embrace technology.
4. A quality-driven ecosystem: Enhancing transparency and collaboration
A quality-driven ecosystem is crucial for maintaining high standards across the supply chain. This involves digital collaboration and interoperability among customers, original equipment manufacturers (OEMs), suppliers, and authorities. Improved transparency and collaboration help minimize defects and improve overall operational efficiency.
For example, an integrated QMS can monitor and improve supplier performance. By analyzing supply chain trends and potential issues, companies can proactively address quality challenges and ensure timely, high-quality deliveries. Digital collaboration tools and data integration platforms allow for seamless communication and data sharing, ensuring all stakeholders are aligned and working toward the same quality goals.
The cost of not maintaining quality is too high to ignore. It’s not just about the financial burden but also about the trust and safety of those who rely on these products. By embracing a quality transformation, companies can improve safety, reliability, and excellence. The future of A&D belongs to those who prioritize quality and harness the power of technology to achieve it. The stakes are high, but the rewards are even higher.
Accenture
https://www.accenture.com
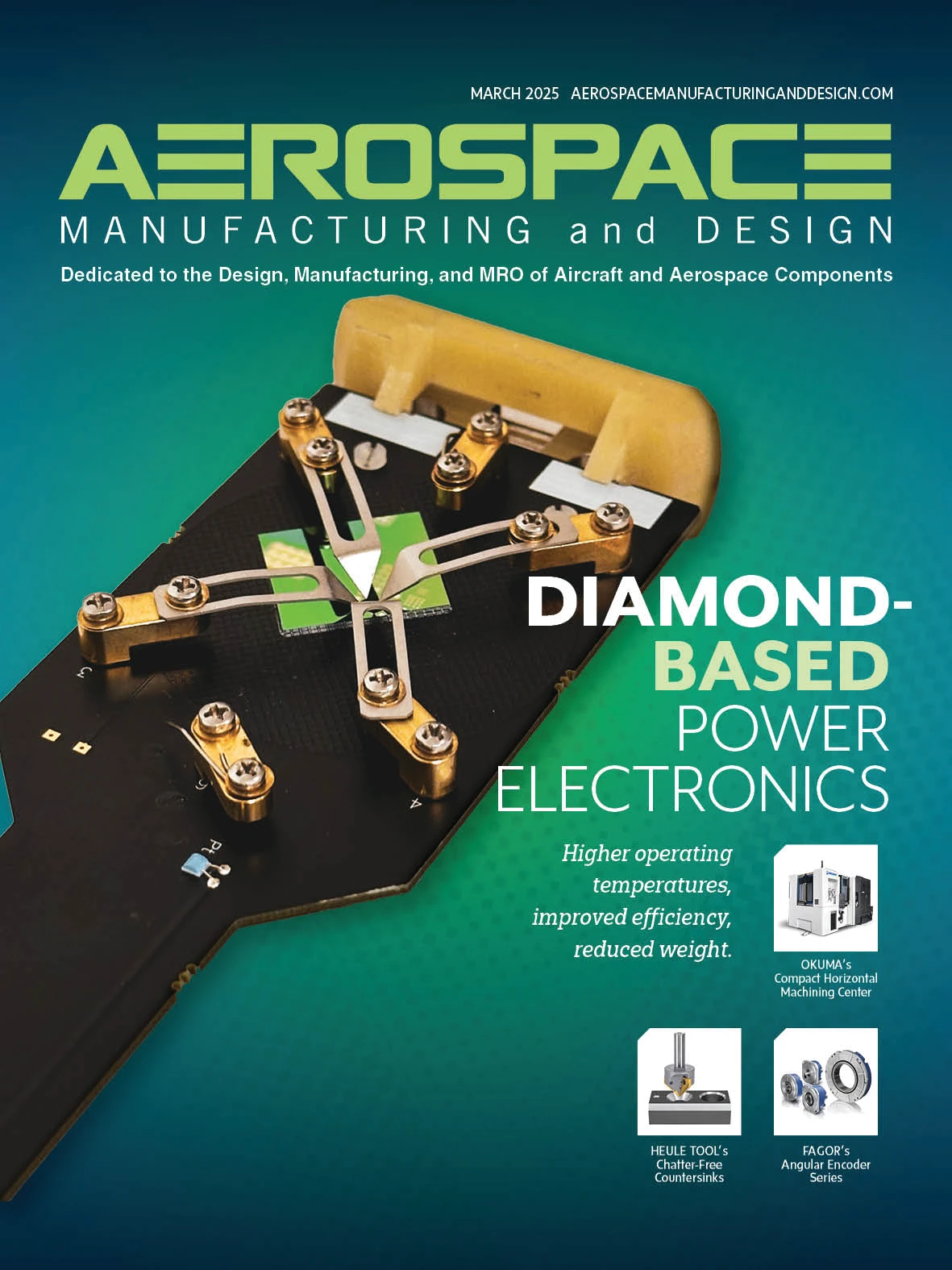
Explore the March 2025 Issue
Check out more from this issue and find your next story to read.
Latest from Aerospace Manufacturing and Design
- Cyient Group, Deutsche Aircraft finalize multi-year contract
- High surface quality at high speed
- #57 - Manufacturing Matters - Agile & Robust Supply Chain Management with Lisa Anderson
- Take control of your manufacturing business despite supply chain turmoil
- Strengthening the defense maritime industrial base for national security, economic resilience
- Register now to learn solutions for high-temperature aerospace machining challenges
- Expertise on machining, joining offered in April’s Manufacturing Lunch + Learn
- NASA offers free high school engineering program this summer