
Teaming up with supply chain partners early and conducting small-stage automated fiber placement (AFP) trials can pay big dividends as aerospace manufacturers increase their use of lightweight composites.
Composite part fabricating variables include:
- Thermoset prepreg, thermoplastic composite materials’ differing properties
- Materials formatted in numerous ways
- Formatted composite processed through various types of AFP equipment
A best practice is for the fabricator, material manufacturer, automation equipment supplier, and material
Effective trials
Ideally, product development will entail a series of small-scale trials with all production partners. Each trial might involve runs at the material supplier’s facility, followed by runs at the precision

Four key early trial benefits stand out.
1. Shorter production lead times – Trials take time, but they shorten the total timeline to market and allow the parties to identify problems and address issues early. Encountering these issues later often leads to costly delays and changes and might even mandate complete redesigns of production processes or equipment.
2. Faster lay-up rates – The rate at which composite materials are applied is critical. Fast material lay-down rates yield greater manufacturing throughout. Early trials allow material formatting and automation processes to be calibrated for the fastest possible lay-up process.
3. Fewer stoppages and changeovers – Continuous operation is just as important as speed. By including precision formatting as part of the product development process, expensive and time-consuming unplanned shutdowns can be minimized.
For example, spool format and sizing are key factors in changeovers. Spool design should be based on part size, production schedule, and out-time constraints for the specific application. If it takes 100ft of composite slit tape to fabricate a part, and six parts are produced per day, spools should carry at least 600ft of slit tape. Otherwise, there will be a need for changeover during a day’s production, causing unnecessary delays. Moreover, if the spool size is wrong for an application, a material management issue can arise with remnant spools or expensive material wasted due to out-time. It seems simple, but even this fundamental type of planning impacts the material manufacturer and the automation equipment
Poor tape quality can also cause downtime. Tapes that have not been properly formatted can have uneven, hairy edges or stringers that can get caught, shutting down the AFP machine. Resolving spool sizing and tape quality issues before production can avert unnecessary stoppages and changeovers.
4. Increased material yield – Material yield usually depends on parent roll specifications versus the formatted tape’s width and length, the manufactured part’s size and shape, and the type of splices acceptable in the finished part; it also involves tradeoffs, such as the choice between wide or narrow composite tape. Wider tape allows more material to be laid down with each
Resolving these issues during product development conserves composite materials, improves the buy-to-fly ratio, and cuts production costs. Conducting early trials allows supply-chain partners to identify and work through challenges and take advantage of opportunities to use new materials, formats, and fabrication methods.
Trial results typically lead to further fine-tuning of the part- fabrication operation so production can begin with the materials, processes, and automation fully validated and ready to roll.
Web Industries Inc.
www.webindustries.com
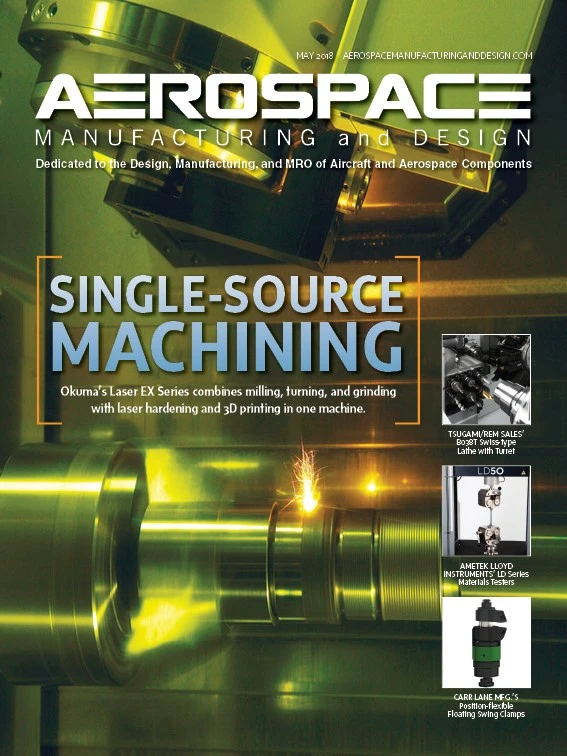
Explore the May 2018 Issue
Check out more from this issue and find your next story to read.
Latest from Aerospace Manufacturing and Design
- Cyient Group, Deutsche Aircraft finalize multi-year contract
- High surface quality at high speed
- #57 - Manufacturing Matters - Agile & Robust Supply Chain Management with Lisa Anderson
- Take control of your manufacturing business despite supply chain turmoil
- Strengthening the defense maritime industrial base for national security, economic resilience
- Register now to learn solutions for high-temperature aerospace machining challenges
- Expertise on machining, joining offered in April’s Manufacturing Lunch + Learn
- NASA offers free high school engineering program this summer