
3D printing has enabled aerospace companies to create complex components previously impossible with traditional techniques. This fosters innovation while reducing costs and turnaround times in a complex, highly-regulated environment.
Due to the typically short runs of parts, the aerospace industry is a prime candidate to benefit from 3D printing. It gives companies the flexibility to print specific aerospace parts for applications in the hundreds or thousands without costly tooling changes. Beyond part production, 3D printing improves manufacturing capabilities for tools that are needed to create those parts. It can also facilitate
Starting the process
How does this process get started? The approach
From there, engineers get involved to see what parts can appropriately be 3D-printed. What follows is a cost analysis to ensure that the parts identified for 3D printing will be produced more
The next step is going to the aerospace organization’s factory to walk the lines to identify pain points and where 3D printing can further assist. Often, we find parts and processes such as jig and drill fixtures that can benefit from 3D printing customization.
Materialise is focused on determining the strength and functional requirements to meet the needs of the highly-regulated aerospace industry. From there, we identify parts, design them with lightweight structures, and run them through 3D printing software to optimize and prepare the files for printing. Unique to 3D printing, mesh/lattice structures allow parts to have the same strength and function with less material, reducing overall weight.


Airworthy parts
In one example of
Another notable collaboration is with 328 Group. The organization handles the maintenance, modification, and refurbishment of its fleet of Do328 commuter airliners. In preparation to re-launch serial production of this aircraft, 328 Group works with Materialise to make plastic spare parts lighter, faster, and less expensively.
While 3D printing has entered the aerospace industry focusing on smaller-scale parts, it is possible that entire aerospace frames could be 3D printed in the future. We are already seeing this in smaller craft and drones, such as the SoleonAgro. Intended for biological pest control in agriculture, it was developed using 3D printing for rapid prototyping, testing, and design verification to reduce the cost of product development. Once designs were finalized, the company turned to Materialise to optimize files with lightweight lattice structures and prepare them for printing. This process gives Soleon the flexibility to design drones to fit various customer needs, from pest control to photography.

Evolving applications
As the industry continues to see the value of 3D printing for aerospace, we also expect companies to begin developing on-site 3D printing operations, which would reduce supply chain, shipping, and storage costs for parts. On-site printing capabilities could also offer real-time design, processing, trial, and implementation of customized parts.
The software and processes for 3D printing with metal are also rapidly evolving, which will have a great impact on aerospace manufacturing processes.
The next 5 to 10 years will be an exciting time to watch this collaboration of aerospace and 3D printing grow stronger. We can’t wait to see where the industry is headed.
Materialise
www.materialise.com
Soleon
www.soleon.it/en
328 Group
www.328group.
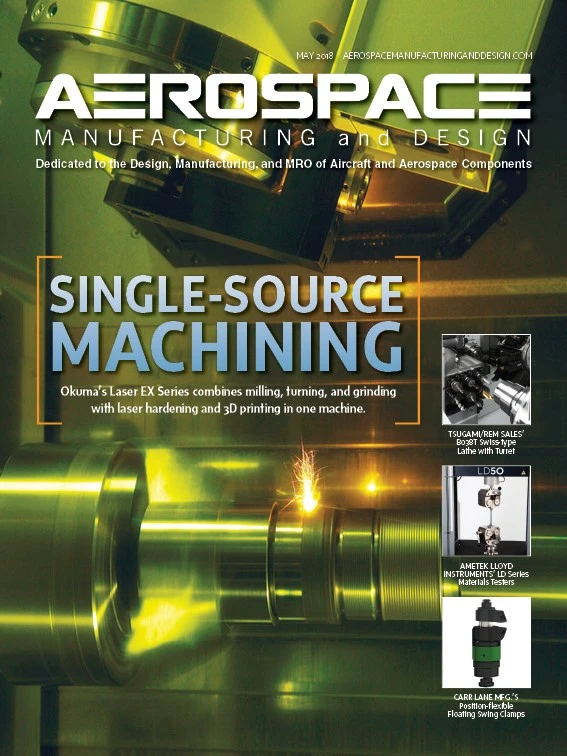
Explore the May 2018 Issue
Check out more from this issue and find your next story to read.
Latest from Aerospace Manufacturing and Design
- Cyient Group, Deutsche Aircraft finalize multi-year contract
- High surface quality at high speed
- #57 - Manufacturing Matters - Agile & Robust Supply Chain Management with Lisa Anderson
- Take control of your manufacturing business despite supply chain turmoil
- Strengthening the defense maritime industrial base for national security, economic resilience
- Register now to learn solutions for high-temperature aerospace machining challenges
- Expertise on machining, joining offered in April’s Manufacturing Lunch + Learn
- NASA offers free high school engineering program this summer