
When BAE Systems became the first aerospace and defense (A&D) manufacturer to incorporate a 3D-printed part in a military airframe, it provided a working example to the world of how the technology could be used in an industry where safety is key. Additive manufacturing (AM) or 3D printing will enable A&D companies to boost production to keep up with ever-increasing demand while keeping to tight budgets. This article looks at how the technology is changing A&D support chains.
AM is quickly becoming a must-have for A&D manufacturers rather than just a luxury research and development project – with the A&D sector now contributing 12% of 3D printing’s $3.1 billion global revenue. A&D companies began experimenting with 3D printing as early as 1988, and industry leaders are now starting to recognize the unique capabilities of 3D printing and searching for ways to exploit them. The U.S. Navy is currently working on 3D manufacturing at sea, which would revolutionize the military support chain, while civil aviation companies such as Boeing and Airbus have been using the process to manufacture components for more than two years.
In the future, 3D printers will allow commercial aviation manufacturers to print parts for aircraft under construction, while defense manufacturers and service providers will produce replacement parts, on-demand, for damaged equipment to support defense operations. Despite the increased uptake of 3D printing in A&D, we have only glimpsed the tip of a large and growing iceberg.
Print spare parts
The complex and specialty nature of A&D equipment makes for a vast support chain. The thousands of constituent parts required to assemble an aircraft or vehicle are typically sourced from companies scattered across the globe. With strict industry safety regulations, this poses a support chain problem for A&D firms, particularly when it comes to maintenance, repair, and overhaul (MRO). With utilization of spare parts a key to keeping assets operational for the maximum amount of time, 3D printing offers a solution.
Spare parts are prime candidates for 3D printing. Demand is hard to calculate at the best of times as most spares must be kept in stock or within reach of procurement at short notice. Production units and spares could be produced on demand, avoiding expensive setups and large quantities of stock – streamlining the entire support chain.
When MRO software indicates a component is faulty or at the end of life span, the availability of a replacement can affect operations. Instead of ordering specialty parts from any given corner of the globe, 3D printing could allow A&D enterprises to access the design electronically and manufacture the required part quickly, cost-efficiently, and crucially, on-site. With the threat of operational downtime negatively influencing revenue, 3D printing offers savings on both fronts.
ROI impact
One of the key inhibitors to large-scale adoption of any new technology such as 3D printing, particularly in the civil aviation sector, is perceived return on investment (ROI). Three-dimensional printing can build parts with designs and structures that help reduce the weight of a part without compromising its mechanical performance. For example, Rolls-Royce and General Electric have shown that they can produce lighter engines more quickly by incorporating 3D printing into their manufacturing process. Both have announced they will produce engine parts through additive manufacturing processes during the coming years. GE Aviation recently became the first OEM to use a 3D printed part to house its T25 sensor – providing pressure and temperature measurements for the control system – and fitted it to more than 400 of its engines currently in service.
When BAE Systems became the first company to create and use a 3D printed part onboard a Tornado fighter jet – a protective cover for the cockpit radio – it made it in one day for less than $150, and with a projected four-year reduction in manufacturing costs of $1.8 million.
Undoubtedly, 3D printing has provided the A&D industry with an enormous opportunity to make and replace parts with accuracy. The time saved when replacing parts out in the field... cannot be ignored.
In theory, 3D printing is hugely cost effective since there is little waste – the process involves adding material rather than chipping it away. On average, AM generates only 5% to 10% waste material – which can be recycled and reused – instead of the 90% to 95% from current machining – a critical attribute when using expensive A&D materials. Again the ROI is plain to see.
As the technology becomes more advanced and affordable, more enterprises in the A&D sector will see the business benefits. A recent study by PwC estimates the MRO market stands to save $3.4 billion annually in material and logistical costs alone. The ROI is clear – AM has the potential to save millions of dollars in manufacturing costs across the A&D sector.
Beware fakes
Comprehensive training around use of 3D printing machines will become a necessity, alongside quality control methods when assessing components manufactured by the process. Three-dimensional printing’s ability to create complex designs and fabricate lightweight but strong structures makes it a natural fit for the A&D industry. However, product quality is the Achilles’ heel of every production technology, and as with all new technologies there are issues that need to be addressed.
The threat of counterfeit parts from easily accessible 3D printers, coupled with the endless amount of designs available on the Internet, could fuel a black market of counterfeit parts. OpSec, a developer of anti-counterfeiting technologies, says online libraries are starting to appear, where object files for 3D printing can be shared on a peer-to-peer basis. This has the potential to severely impact the support chain costs, enabling anyone with the technology to sell counterfeit parts at a discount and leave unsuspecting businesses at risk of poorly performing and dangerous parts. A report from the Organization for Economic Cooperation and Development (OECD) put the value of counterfeit goods that crossed international borders at more than $250 billion as far back as 2007, (http://goo.gl/7tjtly) while the International Chamber of Commerce expected the value of counterfeit goods globally to exceed $1.7 trillion in 2016. (http://goo.gl/58NAAD)
_fmt.png)
While 3D printing is being welcomed in the A&D industry, it will also require key changes in enterprise resource planning (ERP) systems to control every element of the manufacturing, maintenance, and support chain processes to manage the possibility of counterfeit parts entering the support chain. This is crucial in an industry as heavily regulated as A&D, and where safety is paramount.
To accommodate this disruptive technology, MRO providers must ensure their supporting software is flexible enough to adopt new technologies such as 3D printing, especially with the arrival of next-generation aircraft and engines and more complex equipment entering the supply chain.
A recent Oliver Wyman report warned that most aviation companies will have to completely overhaul their information technology (IT) systems to accommodate the changes 3D printing will bring. The research firm expect these innovations will fundamentally change the A&D industry, with printing and manufacturing making up to 20% of the industry’s revenue, or $15 billion. MRO providers face being left behind as 3D printing overtakes traditional manufacturing practices. To take full advantage of the benefits 3D printing can bring, A&D organizations must start preparing now or risk losing out on profit.
AM puts ERP center stage
As more A&D organizations embrace 3D printing, IT infrastructure will have to adapt and integrate – and quickly. Traditional ERP solutions can take months or even years to install, let alone adapt to an entirely new production process, such as 3D printing, which has a dramatic and immediate effect on the support chain, safety, and the whole MRO operation. Companies will need to consider a few things before implementing 3D printing into the enterprise.
Organizations will need process manufacturing elements in their ERP application as the technology effectively combines materials to create something new. Maintaining records of each part produced will be more important than ever as the threat of counterfeit parts entering the supply chain increases. While inventory for spare parts may be reduced, a comprehensive ERP solution will have sufficient forecasting functionality to determine the amount of materials used throughout a certain period. Elements of enterprise asset management (EAM) should also be included to ensure consistent maintenance has been performed and to facilitate regular quality check of printed parts to determine if they meet performance and safety standards.
Modular, application-based ERP solutions remove the time and pain required to modify processes and make it possible to deploy new technology quickly. These agile ERP systems are far more able to accommodate new technologies such as 3D printing in a way that will allow operators to streamline the support chain, reduce time-related costs, and reduce maintenance turnaround times.
Undoubtedly, 3D printing has provided the A&D industry with an enormous opportunity to make and replace parts with accuracy. The time saved when replacing parts out in the field, as well as the potential manufacturing and support chain cost savings, cannot be ignored. But in order to integrate new manufacturing processes such as 3D printing, A&D organizations need to be able to easily customize and adapt their IT infrastructure. Agile ERP software becomes even more vital to manage MRO.
IFS
About the author: Kevin Deal is vice president for Aerospace & Defense at IFS. He can be reached at kevin.deal@ifsworld.com.
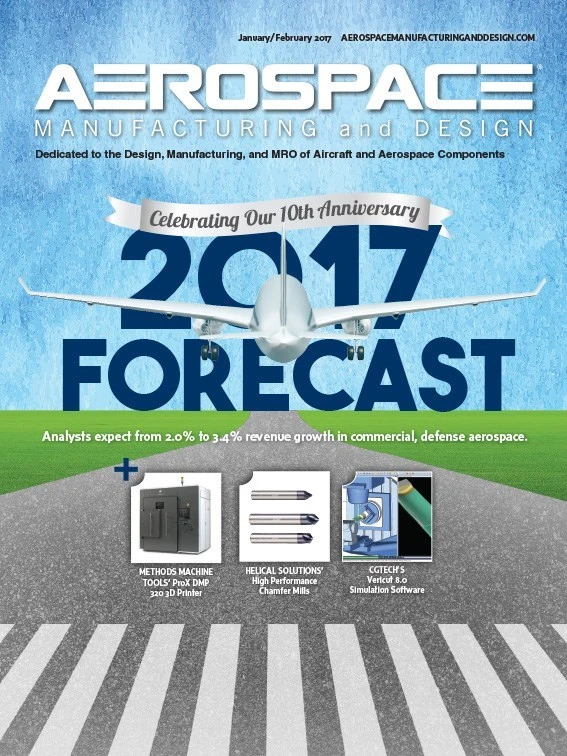
Explore the January February 2017 Issue
Check out more from this issue and find your next story to read.
Latest from Aerospace Manufacturing and Design
- Boeing to build US Air Force’s sixth-generation fighter jet
- Sandvik Coromant introduces CoroMill Plura barrel
- #54 - Manufacturing Matters - HMI Solutions for EV Industry from EAO
- Aerospace Industry Outlook returns for spring 2025
- Drop in for an interactive webinar on automation in manufacturing
- SW’s wing rib technology for the aerospace industry
- Mach Industries launches Mach Propulsion
- Murata Machinery USA's MT1065EX twin-spindle CNC turning center