
GE Aviation later received U.S. Federal Aviation Administration (FAA) approval to produce AM fuel nozzles – the first on-aircraft production part – for the LEAP engine.
This nozzle demonstrates the benefits that can be delivered by AM components – parts per nozzle were reduced from 20 to one; overall weight was reduced by 25%

Boeing is now 3D printing titanium parts for the 787 Dreamliner, which will be the first printed structural components designed to bear the stress of an airframe in flight. With this approach, Boeing can save up to $3 million per jet.
The capabilities of AM technologies are introducing a new world to manufacturing, providing cost savings, labor savings, weight reductions, and part simplification – changes that could significantly impact the supply chain. Parts and sub-assemblies typically die cast and/or machined as separate pieces can now be 3D-printed as a single item. Fewer parts and sub-assemblies mean less tooling and labor, reducing processes along the manufacturing chain and speeding time to market.
Steps in today’s production scenario include designing the production part, designing the equipment and molds to produce a prototype, testing the prototype, revising the prototype and the tooling, and repeating the process. AM eliminates the time and expense for tooling and retooling, moving directly to prototype. Prototype updates can be made in CAD files, allowing companies to quickly make multiple design iterations. According to a Deloitte study (see sidebar below), research has shown that when aerospace and defense (A&D) companies switch from traditional manufacturing to AM, time savings in prototyping range from 43% to 75%. This is important to an industry where backlogs have become the norm.
AM can also greatly lower inventory levels. To avoid the potential of any plane being grounded, airline companies stock spare parts that may go unused or become obsolete. AM eliminates this need as companies can 3D
With these advantages, the 3D printing market is expected to surpass $4 billion by 2023, according to management consulting company Roland Berger. It’s easy to get excited about all this potential, but important to note that despite the advantages, AM also has a set of challenges.

AM roadblocks
From a design standpoint, AM has its own particularities. Design freedoms typically refer to terms of geometry, so there are many other variables and constraints to consider. For example, small changes in process parameters – such as material storage temperatures and humidity – affect the microstructures of the deposited material and change how the end product behaves.
Currently, there are no formal standards for efficiently ensuring product viability of AM-mass produced components. Before manufacturers can invest in 3D printing aircraft parts, they must be able to certify repeatability and predictability of the process to consistently create reliable parts that meet specifications. This cannot be accomplished without strong simulation capabilities that capture the physics of the material and the process.
New materials typically require new manufacturing methodologies. And with AM, current CAD programs are limited, especially when integrating with simulation information. The process is typically manual and requires multiple iterations. These issues illustrate the importance of having AM development tools that are part of an end-to-end digital strategy with simulation embedded within the
Additionally, a future manufacturing strategy with AM as a core resource will reduce inventory, improve material flow, and enable efficiencies through just-in-time inventory management. This also deems the importance of an end-to-end infrastructure that provides digital visibility across the enterprise’s manufacturing operations inclusive of its suppliers, providing manufacturers with opportunities to create value for suppliers.
AM offers aircraft manufacturers the opportunity to streamline the supply chain, producing highly customized aircraft parts and printing more efficient, lightweight materials. To gain the full benefits of AM, design and manufacturing processes must fundamentally change to enable quicker production processes that result in consistent quality on a large scale, and ultimately support the future of aviation innovation.
Dassault Systèmes
https://www.3ds.com
About the author: Rani Richardson is director, CATIA Technical Sales for Light Weight Engineering at Dassault Systèmes.
Resources
Get curated news on YOUR industry.
Enter your email to receive our newsletters.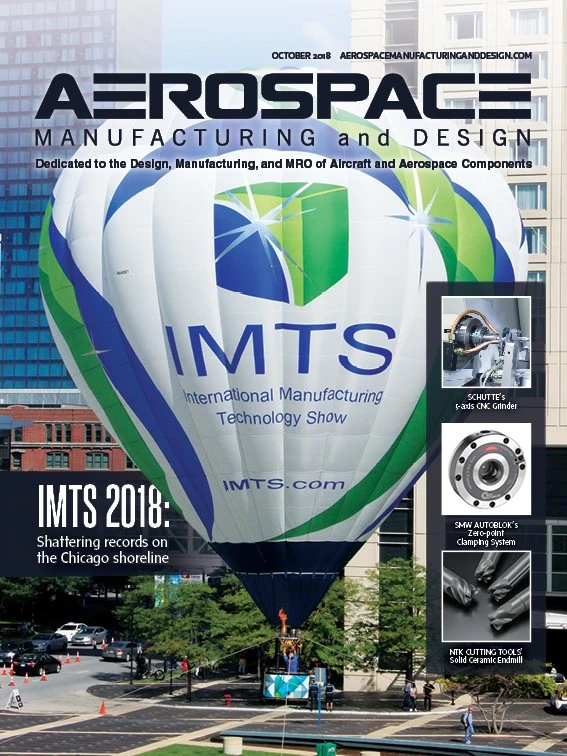
Explore the October 2018 Issue
Check out more from this issue and find your next story to read.
Latest from Aerospace Manufacturing and Design
- Mastering high-temp alloys with Kennametal Inc.
- Boeing to sell portions of digital aviation solutions
- SMW-Autoblok’s KNCS-matic 3-jaw power chuck
- 3 Questions with an Expert with Allied Machine & Engineering
- Electra raises $115M to pioneer Ultra Short aircraft
- Walter’s WT26 partial- and full-profile thread turning inserts
- April Manufacturing Lunch + Learn with Iscar
- April Manufacturing Lunch + Learn with Insaco