
Airbus’ additive layer manufacturing initiative groups experts and competencies from the aircraft manufacturer’s engineering, manufacturing engineering, and procurement operations to define a vision, strategy, and roadmap for applying 3D printing technologies.
This approach will accelerate the company’s technical and industrial competencies and apply research and technology to programs, says Jerome Rascol, who heads the initiative.
“I can see Airbus manufacturing a ‘bionic’ aircraft based on 3D printing in the future, so we’re taking a pragmatic, step-by-step approach,” he says.
Airbus already uses 3D-printed parts on commercial jets – from the widebody A350 XWB to its single-aisle A320neo and the A300/A310 family. The A350 XWB program uses about 2,700 3D-printed plastic parts. Airbus also is working with the European Aviation Safety Agency (EASA) to qualify titanium components produced with 3D printing technology.
Additive manufacturing technology also has been used to produce pylon components for the A320neo (new engine option) developmental aircraft in support of the flight test campaign, and for out-of-production spare parts on the A300/A310 family of jetliners.
With Airbus’ additive layer manufacturing initiative, Rascol says, “There are surely applications and paradigm changes we have not thought of yet. We are thinking every day about ways to 3D print tomorrow’s technology for airframes, cabins, and systems.”
This strategy focuses on developing methods, tools, and training for 3D printing; supporting the application of additive manufacturing technologies in Airbus’ supply chain; and cooperating with airworthiness authorities to qualify materials and processes for certification. www.airbus.com
New polymers for 3D printing
Materials solutions provider Victrex is leading a consortium of companies and institutions pursuing innovation in 3D printing. As part of its role, Victrex will develop new grades of high-performance polyaryletherketone (PAEK) polymer based on chemical formulations designed to work in additive manufacturing processes. Although already used in some additive applications, current PAEK materials were developed for injection molding or extrusion processes.
The new grades target the aerospace industry, the consortium’s main focus. Possessing intellectual property covering the new polymers being developed, Victrex was awarded funding from the U.K.’s agency for innovation, Innovate UK, to help drive the project. Other members of the consortium are Airbus Group Innovations, EOS e-Manufacturing Solutions, University of Exeter, E3D-Online, HiETA Technologies, South West Metal Finishing, and Avon Valley Precision Engineering.
A key objective is improving the recycle rate for laser sintering powders. This would significantly reduce polymer waste in this additive manufacturing process and reduce costs. The project will also address unpredictability of inter-layer adhesion and parts surface finish in filament-based printing.
“Everyone is keenly aware that additive manufacturing has the potential to revolutionize industrial production, since it no longer involves the high tooling and set-up costs of traditional manufacturing,” notes Victrex CEO David Hummel. “High value, lower-volume applications such as aircraft components are the type of application that could benefit the most.”
Victrex’s PAEK polymer, polyetheretherketone (PEEK), is already being used for 3D-printed parts in filament fusion and powder-based laser sintering.
By 2018, Victrex engineers hope to have technology demonstrators that represent proof points and a way forward to realizing all the advantages of additive manufacturing – including reduced costs and a faster time-to-market for products that include parts too complex to be manufactured using traditional methods.
“Although this consortium is a multi-year program, companies who see a value for the benefits of PEEK polymer combined with the value propositions for additive manufacturing should contact us now to discuss their ideas,” Hummel says. www.victrex.com
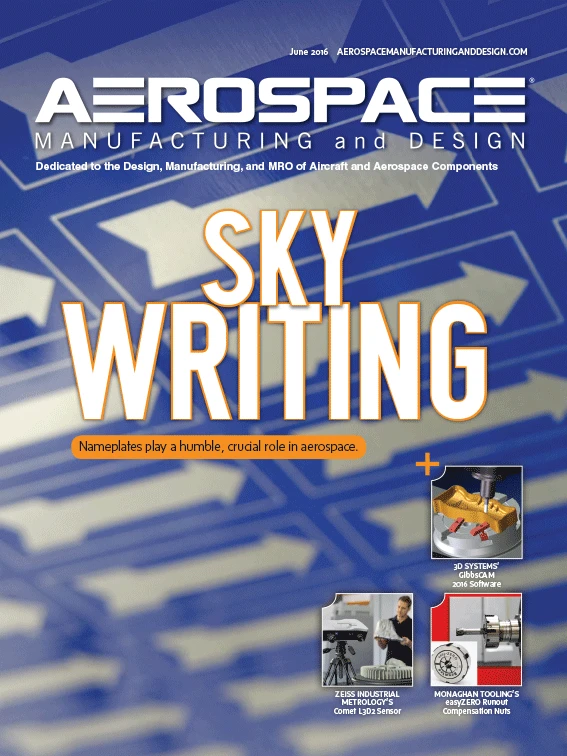
Explore the June 2016 Issue
Check out more from this issue and find your next story to read.
Latest from Aerospace Manufacturing and Design
- Revitalizing the Defense Maritime Industrial Base with Blue Forge Alliance
- Safran Defense & Space opens US defense HQ
- Two miniature absolute encoders join US Digital’s lineup
- Lockheed Martin completes Orion for Artemis II
- Cylinder CMMs for complex symmetrical workpieces
- University of Oklahoma research fuels UAS development
- Motorized vision measuring system
- Everyone's talking tariffs