
Manufacturers may soon be able to 3D print graphene, a lightweight, high-performance material, thanks to researchers from Virginia Tech and Lawrence Livermore National Laboratory.
Previously, researchers could only print graphene in 2D sheets or basic structures. However, a new method allows them to 3D-print graphene objects at a resolution an order of magnitude greater than printed before, theoretically unlocking the ability to create any size or shape of graphene.
Because of graphene’s strength and its high thermal and electricity conductivity, 3D-printed graphene objects would be useful for aerospace, batteries, separation, heat management, sensors, and catalysis.
The material has a single layer of carbon atoms organized in a hexagonal lattice. When graphene sheets are neatly stacked on top of each other and formed into a three-dimensional shape, it becomes graphite.
Graphite has poor mechanical properties, but if graphene sheets are separated with air-filled pores, the three-dimensional structure called a graphene aerogel can maintain its properties.
“Now a designer can design three-dimensional topology comprised of interconnected graphene sheets,” says Xiaoyu “Rayne” Zheng, assistant professor with the Department of Mechanical Engineering in the College of Engineering and director of the Advanced Manufacturing and Metamaterials Lab. “This new design and manufacturing freedom will lead to optimization of strength, conductivity, mass transport, and weight density that are not achievable in graphene aerogels.”
Previously, researchers could print graphene using an extrusion process, similar to squeezing toothpaste, but that
“There’s no support, and the resolution is quite limited, so you can’t get freeform factors,” Zheng says. “What we did was to get these graphene layers to be architected into any shape that you want with high resolution.”
The project began three years ago when Ryan Hensleigh, now a macromolecular science and engineering Ph.D. student, began an internship at the Lawrence Livermore National Laboratory in Livermore, California, working with Zheng, then a member of the technical staff.Hensleigh started with graphene oxide, a precursor to graphene, crosslinking the sheets to form a porous hydrogel. Breaking the graphene oxide hydrogel with ultrasound and adding light-sensitive acrylate polymers, Hensleigh used projection micro-stereolithography to create a solid 3D structure with graphene oxide trapped in the long, rigid chains of
Hensleigh says other processes can print down to 100µm, but the new technique allows him to print down to 10µm resolution, nearly the size of graphene sheets.
Zheng, Hensleigh, and the other researchers are funded by an Air Force Young Investigator Award and the National Science Foundation.
Virginia Tech,
College of Engineering,
Dept. of Mechanical Engineering
http://www.me.vt.edu
Lawrence Livermore National Laboratory
https://www.llnl.gov
Get curated news on YOUR industry.
Enter your email to receive our newsletters.
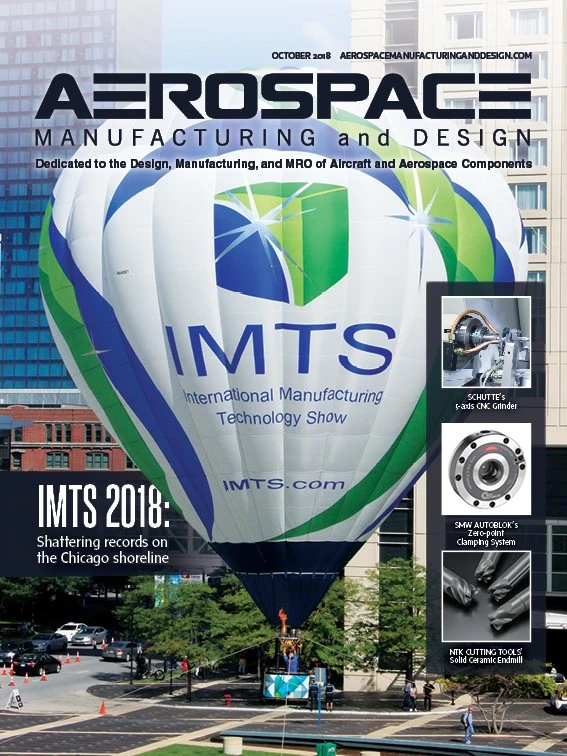
Explore the October 2018 Issue
Check out more from this issue and find your next story to read.
Latest from Aerospace Manufacturing and Design
- Aerospace Industry Outlook - Spring 2025, presented by Richard Aboulafia
- Panama’s National Air and Naval Service selects Embraer Super Tucano
- Model 5770 Linear Abraser
- #42 Lunch + Learn Podcast - Quell Corp
- RECARO Aircraft Seating showcases advanced comfort solutions at AIX 2025
- Mitutoyo America’s MiSTAR 575 Shop Floor CNC CMM
- Korean Air finalizes Boeing widebody order
- Walter introduces a performance copy milling grade