
In 2019, Exploration Mission-1 (EM-1) will be the first of a series of missions that will carry humans farther than they have ever gone into deep space – and eventually to Mars. The Orion will experience extreme temperatures and pressures; harsh conditions that demand advanced thermal control systems to maintain adequate temperatures to ensure crew and spacecraft survive the voyage.
EM-1 and other missions under extreme conditions are pushing innovation in thermal management. Next-generation aerospace thermal management systems require more performance, less weight without pressure loss, modularity, and scalability.
Additive manufacturing (AM) can produce thermal management systems for prototypes and production parts that launch into space, enabling complex, mission-critical thermal control components that are smaller and lighter than machined pieces.

Applications for thermal management
AM can support the development and manufacturing life cycles of thermal control systems in many ways. Proof-of-concept work with additive plastics or metals uses models that can be 3D printed, allowing engineers to validate designs and move onto new iterations rapidly. PolyJet 3D printing technology prints in high resolution and full color, allowing engineers to analyze heat flows on components with complex geometries.
Moving into production, direct metal laser sintering (DMLS) can build complex thermal management parts in a range of metals, producing strong, durable, thermally conductive features, including:
- Regenerative cooling channels – Conformal channels in rocket nozzles; produces a monolithic component with internal coating
- Passive heat pipes – Wicking structures can be optimized
in long-range space, small satellite applications - Nonlinear heat pipes – Curved, angled heat can integrate wicking structures into system’s interior
- Microchannel and jet impingement strategies – Higher feature resolution boosts performance of microchannel, thin film, jet-impingement structures, cooling combustion liners, turbine blades, stators, bearings
- Lattice structured thermal shielding – Incorporated into thermal shielding components with AM; creates passive barrier for heat conduction in the part

AM materials for thermal management
The selection of materials for AM is growing, including powder metals for DMLS technology. Additive aluminum (AISi10Mg) and additive copper (C18150) alloys have mechanical properties similar to cast aluminum and wrought C18150 after processing and heat
Copper C18150, a chromium zirconium copper (CuCr1Zr), the latest material in AM for spacecraft, uses
Copper is suitable for integrated regenerative cooling of rocket engines because of its high strength and high thermal conductivity, and AM can readily create internal conformal channels within a rocket nozzle. Copper is also used for microchannel and jet impingement strategies optimized for microelectronic device cooling, as well as conformal induction coils.
Design considerations
During DMLS, parts are built with a laser that selectively heats and fuses powdered metal into layers. The part remains fixed to a base plate with support structures that must be CNC machined off the plate post-build. Consider these guidelines when designing thermal control components:
- Wall thickness – DMLS struggles to build walls thinner than 1,000µm (0.039")
- Feature detail – Complex features with thin walls or channels may need support structures; design should consider powder removal strategies
- Surface Finish – Cleaning/Finishing process (conventional, chemical, electric chemicals machining; mechanical tumbling; abrasive blasting) remove surface material, so feature walls must be thick enough to withstand
post processing
Maintaining acceptable temperature ranges requires advanced engineering and design coupled with the ability to produce complex geometries. AM’s design freedom, growing capabilities, and
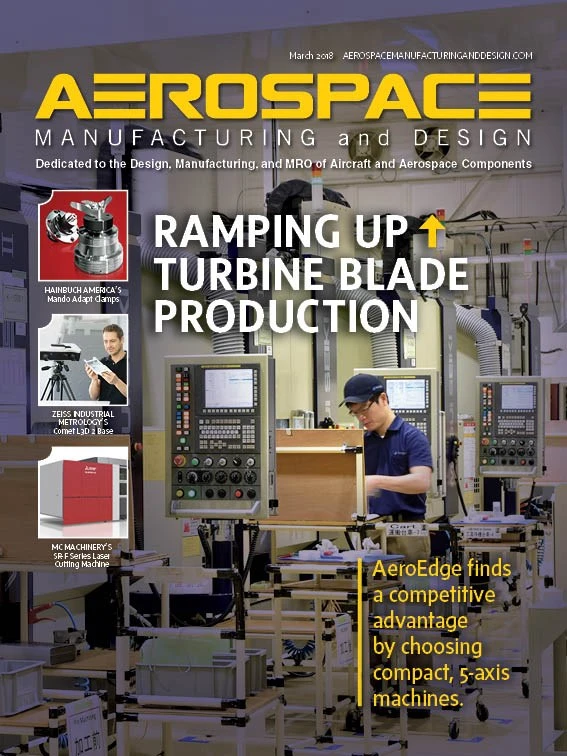
Explore the March 2018 Issue
Check out more from this issue and find your next story to read.
Latest from Aerospace Manufacturing and Design
- GE Aerospace secures Air Force engine contract
- Thomson Industries' online sizing and selection tool
- #53 - Manufacturing Matters - 2024 Leaders in Manufacturing Roundtable
- Join us for insights on one of the hottest topics in manufacturing!
- You can still register for March’s Manufacturing Lunch + Learn!
- Ohio creates Youngstown Innovation Hub for Aerospace and Defense
- Tormach’s Chip Conveyor Kit for the 1500MX CNC Mill
- How to Reduce First Article Inspection Creation Time by 70% to 90% with DISCUS Software