
Maurice J. Zucrow Laboratories

Supersonics denotes aircraft breaking the sound barrier at Mach 1 and extends to around Mach 5; 5x the speed of sound and more than 3,500mph at sea level.
Researchers at Purdue University are learning that exploring the hypersonic environment is a perfect proving ground for metal 3D printing. Recent work demonstrates advanced additive manufacturing (AM) technology is now capable of producing fully dense, end-use parts with robustness surpassing traditional methods such as casting.
Bizarre world of hypersonics
“There’s a line you cross at around Mach 5,” says Purdue Associate Professor Carson Slabaugh, whose team at Zucrow Laboratories has studied high-speed combustion systems since he started his lab at Purdue in 2015. “When a vehicle flies that fast, extreme compression and heating of the air flowing around and within the fuselage occurs. At Mach 5, it’s about a six-fold increase in the temperature and a pressure increase of a few hundred times. That kind of thermal and mechanical loading causes the regime of aerodynamics and thermodynamics and structural mechanics to completely change compared to lower- speed systems.”
According to Slabaugh, this means coming back through the atmosphere in response to gravity, “You’re traveling through a fireball at hypersonic speeds.” This happens when astronauts return to Earth from the International Space Station and is why they are protected by massive heat shields.
If you want to achieve powered hypersonic flight with a controllable aircraft, unmanned vehicle, or missile, you need to add an engine.
Above Mach 5, the temperature of atmospheric air as it rushes by is thousands of degrees and the pressure is several hundred psi. The air can become chemically reactive if you fly fast enough. The extreme flow conditions become a challenge to vehicle-propulsion systems whose thrust comes from burning fuel.
“If the incoming air is too hot, you really can’t add more useful energy to the flow by burning fuel. Dissociation effects become very strong, and the reactions cannot proceed to completion,” Slabaugh says. “Cooling also becomes exceedingly difficult at these flight speeds.” To avoid what rocket scientists call unplanned rapid disassembly, the team at Zucrow Labs focused on learning about the critical turbulent (reacting) flow physics that must be accounted for when an engine reaches hypersonic speeds.
The team partnered with Velo3D to 3D print fuel injectors with complex geometries achieving very high fuel-air mixing performance. The parts couldn’t have been made with conventional fabrication methods, especially not with the high-temperature, high-strength metal superalloys needed to survive the extreme testing conditions. The teams worked to rapidly prototype the Purdue team’s designs for testing, evaluation, and iteration. Slabaugh’s team used the data from the prototypes to scale up their designs into a full-scale system.

Relying on earthbound solutions
Because designing and manufacturing parts for hypersonic conditions is expensive, much of the R&D for developing hypersonic capabilities has been supported by NASA and defense-level budgets. Flight testing the systems is expensive and has major limits on what can be measured for research purposes. Engineers lean heavily on earthbound solutions to develop new technologies while keeping costs in check. They’re recreating conditions experienced during hypersonic flight and proving engine components in ground-test facilities.
“We engineer components that’ll experience hypersonic environments while going zero miles per hour and staying bolted to the ground,” he says. Advanced computer simulation software has been a valuable tool for engineers exploring the relationship between complex physics and physical structures. Methods such as computational fluid dynamics (CFD) and fluid-structure interaction (FSI) can simulate material and structural behavior in response to the flow of air or liquid, allowing engineers to optimize designs before ever manufacturing anything.
Hypersonics are extremely unpredictable, defeating the most sophisticated computer-simulation capabilities.
“One fundamental problem is that we can’t reliably predict the flow and flame conditions within the engine at hypersonic conditions,” Slabaugh says. “Reacting, turbulent-flow is extremely complicated to model with CFD; we’re at such extreme levels of turbulence and flow conditions we can’t capture everything happening as the flame evolves. Within the flow you have evolving density, viscosity, velocity, species and, when you add in mechanical structures such as engine walls to contain the flame, you get more complicated with cooling designs affecting the flow and flame. The computational power you need to analyze the smallest part of the engine is expensive and the result is many assumptions must be made for integrated design analysis.”
Solution for hypersonics-worthy parts
So how do you get engineers unstuck from this problem? Leave simulation behind and go back to the real-world, classic, manufacturing paradigm of build and break, and use advanced metal AM for the build part.
“We’re working on a very large 3D-printed burner, to create the hypersonic flow environment on the ground in a test cell,” Slabaugh says. “If you want to test a hypersonic vehicle on the ground you build a rocket engine with a big converging-diverging nozzle and a supersonic plume of extremely hot gas; the fireball the vehicle is flying through. The whole system is bolted down into concrete. You stick components you’re designing inside the plume and watch what happens.”
Slabaugh’s team designed the injectors for the combustor to produce specific turbulent flow fields mixing fuel at a certain rate and allowing stabilization of a powerful flame in a very compact volume, creating the conditions for the things they’re going to test.
Quickly 3D printing injector geometries for the test combustor made of high-temperature-resistant superalloy Hastelloy X enabled the Purdue team to rapidly identify the best designs.
“We had approached this problem with traditional subtractive manufacturing techniques before,” says Nick Strahan, test engineer on Slabaugh’s team. “But there were features in our design that limited the performance of the combustor and doing it additively enabled us to integrate our unique geometry much more easily.”

Swerving past traditional manufacturing
Using traditional subtractive manufacturing would’ve meant casting individual parts, requiring long, drawn-out cycles of tooling, moldmaking, and design iteration.
The engineers varied the flow passages of the injector with 5 different designs, printed them, and ran them through hypersonic-relevant test conditions.
The team could isolate the highest performer having the stationary and dynamic features they were looking for in 2 weeks.
The high-performance injector met the critical parameters the engineers valued most for performance of the combustor: flame power as a proxy for the simulated flight conditions and flame stability, a metric for the health and efficiency of the combustor.
Maurice J. Zucrow Laboratories at Purdue University College of Engineering
NEWS AND PRODUCTS
Automating production monitoring for Universal Robots

Datanomix, maker of the Automated Production Intelligence software platform, will monitor Universal Robots (UR) for real-time visibility into robot performance. By partnering with Flexxbotics, a leader in robotics process improvement technology, Datanomix extends its Automated Production Intelligence coverage to UR cells, helping power lights-out and automated operations at precision manufacturers.
Datanomix gains access to real-time operational data for UR from Flexxbotics via its FlexxConnect platform. Advanced utilization and performance data for UR is collected and displayed in the Datanomix platform, offering insights into cobot and CNC machine cycle time, part counts, run time, and machine/robot status so precision manufacturers can make better-informed decisions around automating the factory. FlexxConnect provides centralized and revision controlled cobot and CNC program management capabilities, and guided workflows for both cobot operators and CNC operators.
Existing Flexxbotics customers can add Datanomix to their deployments and Datanomix customers can add the Flexxbotics management platform to UR installations. Using Flexxbotics’ underlying technology, the Datanomix platform receives performance information directly from UR, visualizing it alongside the performance data from the CNC machines the robots empower.
The Datanomix Platform automates collection and analysis of manufacturing data, delivering deep insights into production performance, in real-time and over-time.
Designed for growth-oriented precision manufacturers, the Datanomix platform delivers manufacturing productivity with no operator input required, and without burdening the end user with cumbersome analysis or data crunching.
The Flexxbotics platform significantly increases cobot tended CNC utilization and productivity through a suite of robot redeployment, robot monitoring, robot to CNC connectivity, guided workflow, and robot/CNC program management solutions.
AI-powered, HD mode for 3D scanners

Exact Metrology, 3D metrology service provider and hardware sales company, increased the capability of Artec 3D handheld scanners with the HD mode. This artificial intelligence (AI)-powered scanning technology provides ultra-sharp, clean, and detail-rich scans for Artec Leo and Artec Eva.
Users can obtain sharp 3D scans with a resolution of up to 0.2mm. Trained on hundreds of thousands of carefully selected samples, the engine’s neural network detects familiar patterns, surface details, and shapes, allowing the scanner to reconstruct a higher number of polygons per frame, resulting in denser and higher quality 3D data. The desired HD density can be selected from a standard 1x density up to 36x for Eva and 64x for Leo. HD mode captures smaller, thinner elements with the 3D scanner while considerably reducing noise. Fine edges can be captured in high definition, faithful to their original shape and it’s easy to capture hard-to-reach areas as scans are reconstructed with every detail, giving users complete surface geometry.
Handheld scanners can scan dark or shiny surfaces in high resolution and capture the full range of geometries without additional steps. Using the Artec AI engine, little to no noise in the raw scan data results in cleaner processed data, saving time when producing the final 3D model. Short hair and separate strands are fully within reach when scanning with HD mode. A perfect fit for reverse engineering and quality control due to clean, comprehensive data, scans can be easily fitted with primitive shapes and exported to the most popular CAD solutions for development.
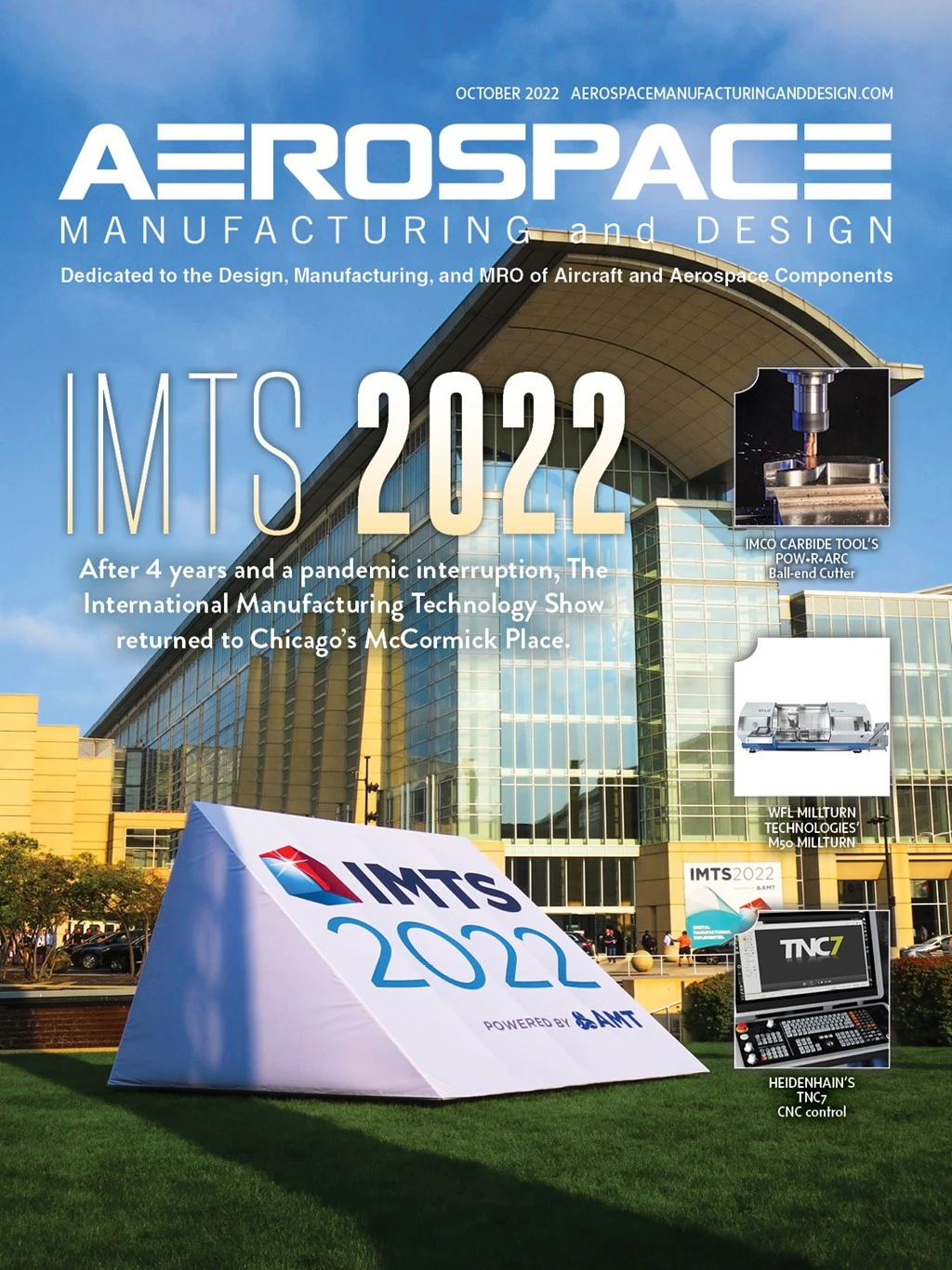
Explore the October 2022 Issue
Check out more from this issue and find your next story to read.
Latest from Aerospace Manufacturing and Design
- Industrial automation products, enclosed encoders
- #61 - Manufacturing Matters: CMMC roll out: When do I need to comply?
- AIX shows aircraft interiors are a strategic priority for global airlines
- Machine Tool Builders Roundtable: Turn equipment into expertise
- No time to waste: How to machine MedTech parts more efficiently
- The 5 Best and Fastest Spindle Repair Services
- Mill smarter, not harder: How collaboration optimizes production
- Be proactive – stay ahead of tariffs and other economic and supply chain curveballs!