
The dust-tight, fully automated 3D-ReKlaimer metal powder recovery system recovers and reconditions used powders to exacting particle sizes – reducing waste and lowering operating costs while preventing product and plant contamination.
The system reclaims metal powders used in selective laser sintering (SLS), fused deposition modeling (FDM), and
Screened powders ready for reuse are discharged into bottles for manual connection to 3D printers or transferred automatically by an integral pneumatic conveyor that discharges into a filter receiver/hopper.
www.kason.com
LPW, APWORKS partner for AM metal powder portfolio
Metal powder manufacturer LPW is partnering with Airbus
Industrial 3D printing market worth $5.66 billion by 2023
According to MarketsandMarkets research report, the industrial 3D printing market is estimated to grow from $1.73 billion in 2018 to $5.66 billion by 2023, at a compound annual growth rate (CAGR) of 27.21%. Driving factors include the evolution of 3D printing from developing prototypes to end-use parts production, ease of developing customized products, developments in existing industrial 3D printing materials market, government investments in 3D printing projects, and improvement in manufacturing efficiency.
North America held the largest share of the market in 2017, followed by Europe and Asia-Pacific (APAC). The U.S. held the largest share of the North American industrial 3D printing market, followed by Canada and Mexico. The presence of major manufacturing, aerospace
Evolving needs of end-user industries and emerging application areas for 3D printed materials are expected to increase the consumption of printing materials, contributing to the market’s CAGR in the next 5 years. Restraints that curb the market are the high cost and limited availability of materials, difficulties associated with the use of 3D printing software, and lack of standard process control.
www.marketsandmarkets.comStratasys partnering with Eckhart, spins off Vulcan lab
Stratasys’ three-year agreement with Eckhart will advance the adoption of 3D printing for factory tooling in North America. The partnership will also promote micro-sensors in 3D printed tools to begin integrating advanced diagnostics for smart factories of the future.
Eckhart’s 3D printing laboratory, in Warren, Michigan, includes printers using Stratasys’ fused deposition modeling (FDM) 3D printing process. The lab uses Fortus 450mc, F370, and Fortus 250mc 3D printers to produce on-demand parts. Eckhart also uses Stratasys’ carbon-fiber-reinforced FDM Nylon 12 CF.
Vulcan Labs Inc., a Stratasys spin-off, is to advance the use of powder-bed fusion (PBF) additive manufacturing (AM) to meet demands of end-use production applications. Aimed at overcoming typical deficiencies of productivity, quality, and certification, the labs’ initial focus will be on metals. Vulcan Labs collaborates with application partners to advance technology accessibility and meet requirements of production-ready applications.
www.eckhartusa.com; www.stratasysdirect.com; www.vulcan-labs.comBoeing , Oerlikon collaborate to qualify materials, processes
Boeing and Oerlikon signed a five-year collaboration agreement to develop standard materials and processes for metal-based additive manufacturing (AM).
Data will support the qualification of AM suppliers to produce metallic components using various machines and materials. The research will initially focus on industrializing titanium powder bed fusion AM and
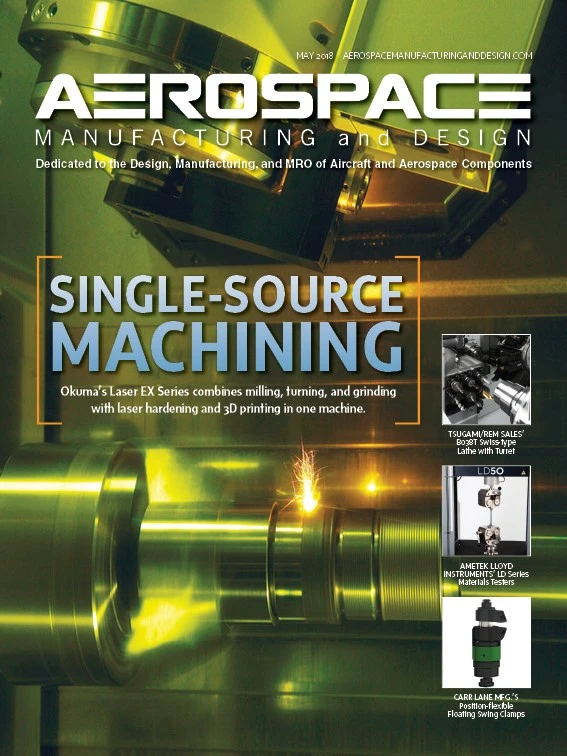
Explore the May 2018 Issue
Check out more from this issue and find your next story to read.
Latest from Aerospace Manufacturing and Design
- Cyient Group, Deutsche Aircraft finalize multi-year contract
- High surface quality at high speed
- #57 - Manufacturing Matters - Agile & Robust Supply Chain Management with Lisa Anderson
- Take control of your manufacturing business despite supply chain turmoil
- Strengthening the defense maritime industrial base for national security, economic resilience
- Register now to learn solutions for high-temperature aerospace machining challenges
- Expertise on machining, joining offered in April’s Manufacturing Lunch + Learn
- NASA offers free high school engineering program this summer