
When working with the complex, difficult-to-machine materials of expensive aerospace components, the choice of tools can be the difference between success and failure. Waste material, frequent tool changeouts, excessive downtime, and scrapped components are signs of inadequate tooling. They’re also signs of unsustainable machining.
Cutting tools can have a major impact on the sustainability of metal cutting operations. It’s an area many machine shops overlook when setting their strategies to meet environmental goals. Fortunately, sustainability and best business practices can go hand-in-hand. With the right tooling, shops can minimize costly mistakes to their business and the environment.
As the world moves to meet net-zero emission goals, the aerospace industry has a big hill to climb, as it’s one of the most challenging industries to decarbonize. While aerospace manufacturers rightly look to innovate their products to reduce aviation’s environmental impact – which accounts for about 70% of emissions in the aerospace industry – they can also make significant gains on the manufacturing side.
Component manufacturers need efficient, economically-sound processes that also conserve energy and critical resources. While innovations such as digital twins, near net-shape components, additive manufacturing (AM), and digital, Internet of Things (IoT)-powered technologies have a role to play, tooling will also have a critical impact on the efficiency of any operation. Here are three ways tooling can help manufacturers reduce their environmental footprint.
The right tools for improving efficiency
For machine shops tasked with cutting difficult-to-machine metals into complex components with tight tolerances and the utmost surface quality, the right tools and expertise are essential. Using tools optimized for heat-resistant super alloys (HRSA) and other difficult materials, or specialized tools designed for more efficient cutting operations, will lead to less wasteful machining processes and support major sustainability benefits.
Scrapped components are a major contributor to manufacturing waste and a major cost to any shop and can have a serious impact on the environment if it isn’t recycled. World Bank estimates that industry produces 18x more waste compared to solid waste municipalities globally.
If machine shops are to reduce scrap, they must implement the right tooling setup and cutting data. Failure to secure these factors can result in irregular tool wear and unpredictable insert tool life, leading to component rejections and, in turn, scrap.

Tool choice is integral to reducing waste in turning. But what are the characteristics of a more reliable tool? Optimized turning grades and geometries providing long, predictable tool life with good chip control should be considered for secure and productive machining. Selecting cutting tools optimized for HRSA can lead to big benefits, such as minimizing unplanned stops or reducing waste from the workpiece material or the carbide insert. These are necessary preconditions for sustainable machining.
Tool reconditioning
Time is money in aerospace manufacturing. Drilling, milling, and reaming place enormous stress on metalworking tools. But there’s an alternative to buying new solid carbide tools every time: tool reconditioning, which can extend a cutting tool’s life cost effectively and sustainably.
The word reconditioned can elicit visions of worn, overworked products inferior to brand-new versions. However, if shops purchase from a reputable tool manufacturer, reconditioned tools can deliver the same consistent results as they did upon initial purchase.
Shops should realize reconditioning isn’t equal to repair. When repairing a piece of equipment, only the defective parts are investigated and replaced. Reconditioning rejuvenates every aspect of the product and brings the part back to its original manufacturing standard. Shops should expect reconditioned products to be in the same, perfect condition as a brand-new part.
Using solid carbide tools isn’t a case of if the tool will wear out, but when. Because of this inevitability, reconditioned tools can help reduce a shop’s total tool expenditure. Shops should look for a tool producer that considers reconditioning from the design phase. Typically, tool CAD data will be stored so reconditioned versions can perfectly match the tool’s original geometry and coating. For custom-made cutting tools, this is essential to meet the original tool specifications.

Shops should learn to identify the types of tool wear to determine which tools are viable for reconditioning. Tool wear can vary depending on the mechanism and cause of wear. The most common tool wear is uniform flank wear resulting from high cutting speed and low feed or low wear resistance. Certain wear may be more viable for reconditioning than others.
Solid carbide tools are often made using several finite raw materials, such as tungsten and cobalt, making multiple repurchases unsustainable. The ability to reuse a single tool multiple times through reconditioning, in place of simply purchasing new tools, plays a major role in sustainability efforts.
Reconditioning can help shops make the most of their tools while extending a tool’s life span – sometimes by up to 3x its expected duration. At the end of the solid carbide tool’s life cycle, some tooling companies have buy-back programs to recycle solid carbide and create new tools.
Reducing packaging
Aerospace machining operations also can reduce waste by choosing a tool provider working to minimize packaging. The most progressive tooling companies are now using advanced artificial intelligence (AI)-based algorithms to optimize packaging for each part to use the least amount of material possible while still effectively protecting the tool.

For example, Sandvik Coromant’s Package Selector Application (PSA) identifies the most critical points of an object by analyzing its CAD-based model in 3D. The AI algorithm then works out the object’s rotation and can recommend the smallest possible packaging and how to fit the object into the selected packaging.
Aside from contributing to lower costs for packaging materials, transport, and storage, the ability to always select the smallest possible package also helps reduce CO2 emissions. Smaller packages take up less space, so more can fit into a shipment, reducing transportation fuel consumption.
Having the right tooling partner can help improve sustainability in your aerospace machining operations. The right tools can make the difference between productive, sustainable metal cutting and a wasteful machining process.
As aerospace shops form and execute more ambitious sustainability strategies, innovations in tooling are being realized to significantly improve a company’s credentials. By seeking the right tools with the right partner, they can find more sustainable ways of machining aerospace components and move the industry forward for people, the planet, and profits.
About the author: Bill Durow is the global engineering project office manager for aerospace, space, and defense at Sandvik Coromant.
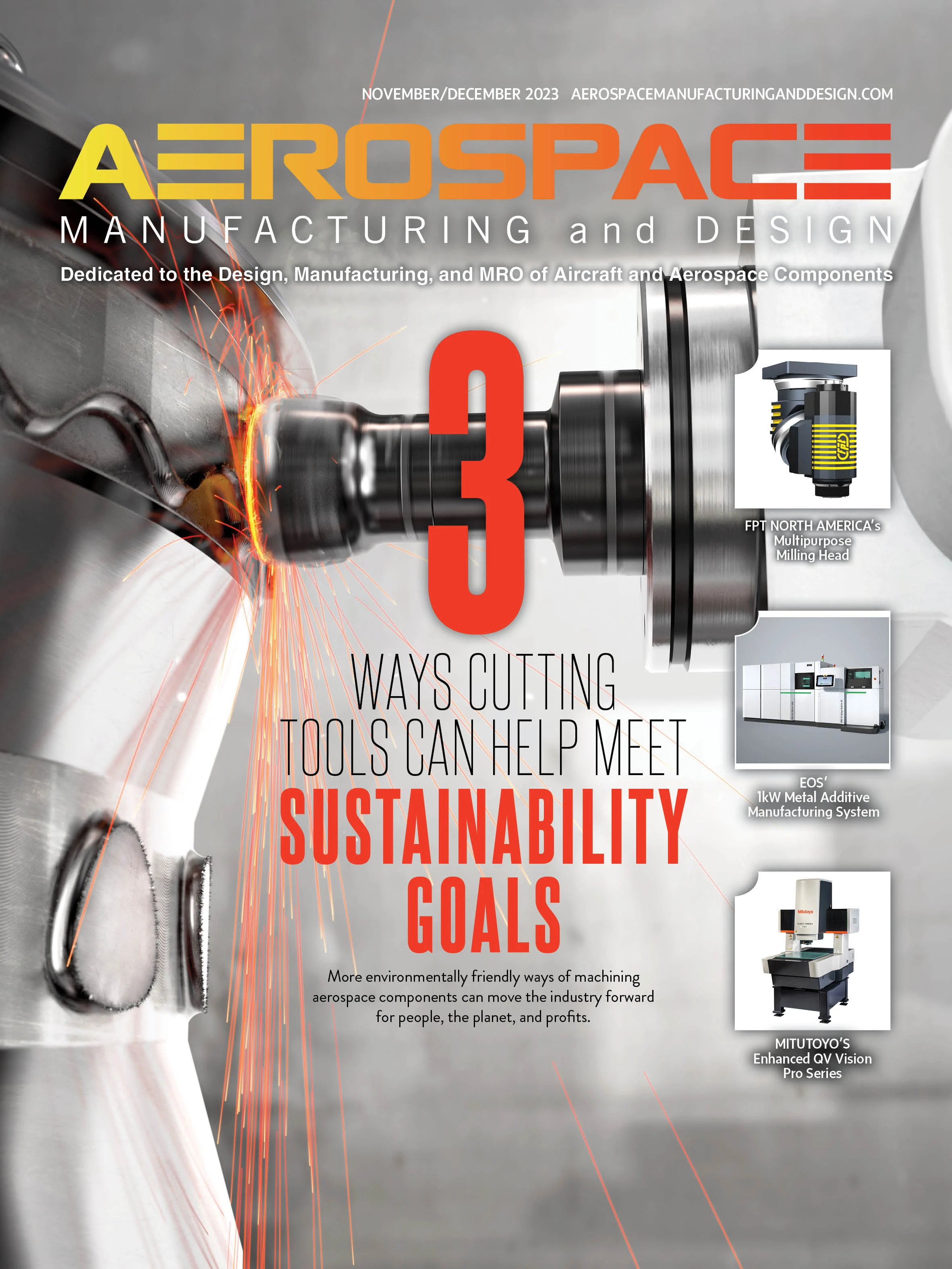
Explore the November December 2023 Issue
Check out more from this issue and find your next story to read.
Latest from Aerospace Manufacturing and Design
- 2024 Favorites: #6 Article – Mastering complex precision machined parts
- 2024 Favorites: #6 News – Boeing to acquire Spirit AeroSystems in $8.3B deal
- Season's greetings
- 2024 Favorites: #7 Article – Deep drawing aerospace components
- 2024 Favorites: #7 News – GKN Aerospace completes sale of St. Louis facility to Boeing
- 2024 Favorites: #8 Article – Beyond uptime
- 2024 Favorites: #8 News – NASA, Lockheed Martin reveal X-59
- 2024 Favorites: #9 Article – 5 tips for upskilling your aerospace machinists