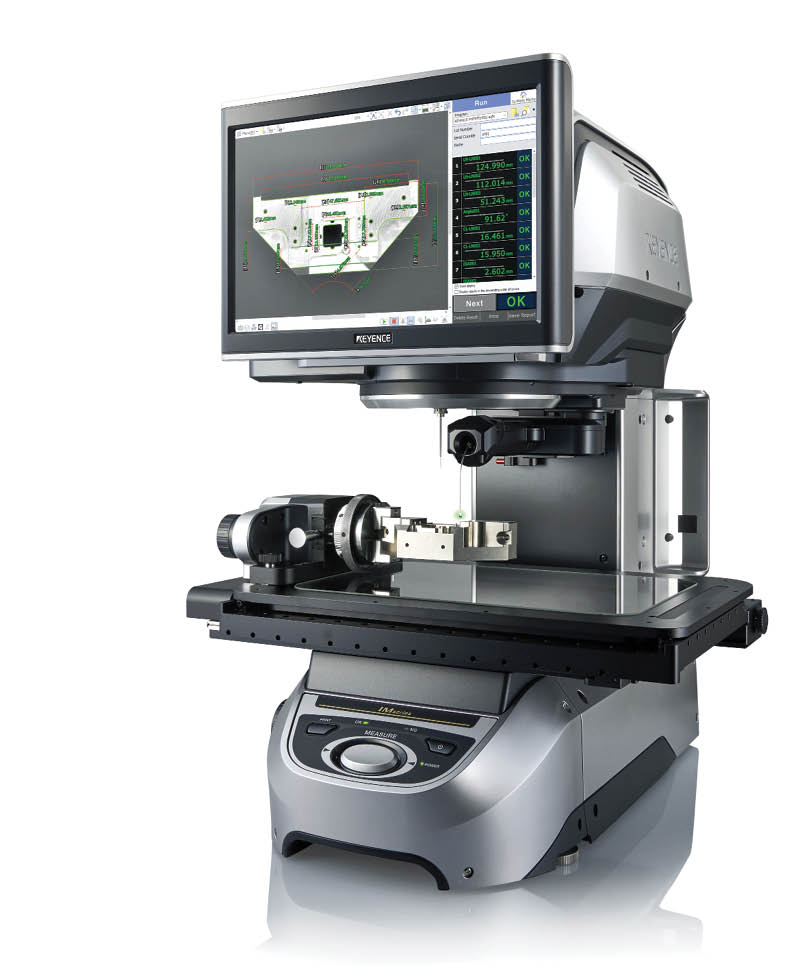
Automation for aircraft manufacturing began in the 1960s for repetitive tasks such as welding, fabrication, painting, sanding, and polishing. This introduction of automation aimed to speed up production and relieve manufacturers from unsafe and time-consuming duties. However, large aircraft components, small production volumes, and aircraft assembly prevent automation from completely taking over manufacturing tasks. Instead, automation for aircraft manufacturing is becoming more intelligent, collaborative, and efficient with the integration of artificial intelligence (AI), the Industrial Internet of Things (IIoT), and larger-scale machines.
Three transformations in automation are included in advanced metrology solutions in instant measuring machines (IMM) and coordinate measuring machines (CMM).
1. Innovations with AI – There are two types: Traditional AI implements patterns and rules programmed and taught by humans. Generative AI figures out its patterns and rules. Both types of AI are currently used in aerospace manufacturing for their speed and real-time feedback.
With an IMM or CMM, the automated optical comparator uses AI to measure the part and analyze it compared to its learned rules and patterns which immediately determine whether the part can continue in the supply chain. In seconds, the measurement system responds with OK for pass or NG for failure.
Without AI, a traditional optical comparator measures an aircraft part much slower. A technician takes the measurement and manually compares it to aircraft industry standards and desired measurements. The technician must use handbooks and internal knowledge to determine whether the measurement is acceptable for continuation in the supply chain.

For now, generative AI is still expanding in automation for aircraft manufacturing. Industry experts look forward to it being more embedded into a company’s standards. For instance, generative AI comparing a measurement and searching through a company-specific, non-public database.
2. IIoT advancements – The aerospace industry follows strict traceability standards to streamline recall, prevent counterfeits, and manage inventory. IIoT advancements are increasing the value of data exchange, allowing immediate organization, analysis, and exchange of traceability data between inspection machines and PCs. This means databases are consistently up-to-date and scouring for problems.
Measuring machines’ data flows to software on a PC to implement statistical modeling, graphing, and creating histograms. Instead of a technician manually collecting inspection data at one time, then analyzing it manually days later, IIoT advancements provide real-time data exchange and analysis.
The measuring machines’ IIoT also incorporates 3D CAD integration for troubleshooting, 3D printing applications, and reverse engineering parts. The 3D CAD model feature allows technicians to see on their screen the differences between a CAD model and a physical part. The software uses color to highlight geometric dimensioning and tolerancing (GD&T) differences in real-time or remotely.

Real-time traceability data provides immediate knowledge of inspection accuracy and efficiency. IIoT’s data flow reveals problematic patterns and inventory counts that multiple parties can access throughout the supply chain.
3. Accelerated production – Automation was originally integrated with aerospace production because of its ability to perform repetitive tasks exponentially faster than human technicians. Now, as automation advances with IIoT and AI, the repetitive tasks reach larger scales per unit. Instead of collecting one piece of data per inspection, machines are now inspecting hundreds simultaneously.
As machines acquire larger batches of data at once, parts are moving faster through supply chains while keeping the same (or better) precision. This decreases the cost per inspection and provides an opportunity to scale for more projects. The IMM collects 300 dimensions on up to 100 parts in seconds. One of Keyence’s customers, Gamma Aerospace, reported its 10-minute hole-to-hole measuring process for 300 holes decreased to seconds with this accelerated technology.
Intelligence is key for accelerated inspections, and implementation of AI and IIoT means the machine is cutting down tedious work. The IMM intelligence searches for, identifies, and electronically orients the parts instead of the technician but a technician must press the button.
Where’s automation heading?
The excitement and momentum for automating aircraft manufacturing aren’t expected to slow down. AI, IIoT, and accelerated machining work together inside machines to produce accurate, efficient, and detailed production results. The demand for aircraft is rising, and automation is a promising way to keep up.

There’s one piece that industry experts aren’t expecting to go away. Human consciousness can’t yet be replaced, and collaboration between humans and robots is still required. Assembling large aircraft components, updating policies, and human perception are still jobs for humans.
Automation and human innovation form an ideal pairing. The inventions humans have yet to discover, combined with intelligent and fast manufacturing, inspecting, and maintaining, foreshadow a bright future.
NEWS AND PRODUCTS
ABB acquires Sevensense
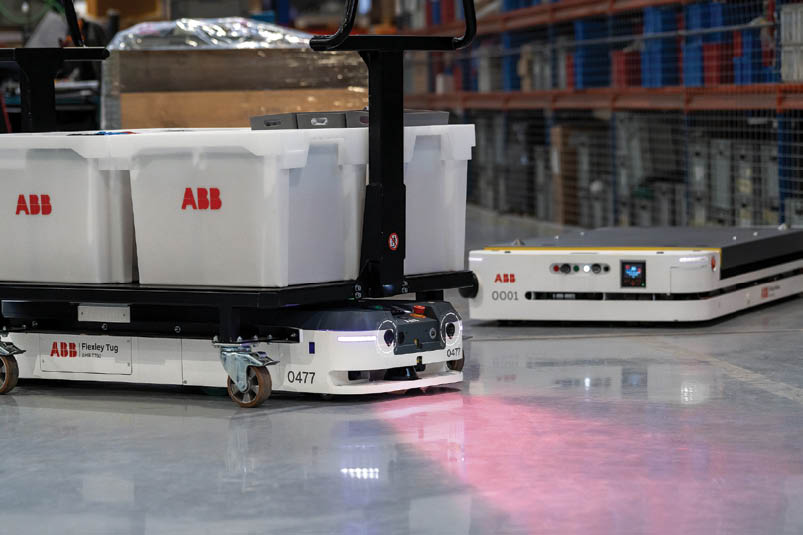
ABB acquired Swiss start-up Sevensense, a leading provider of artificial intelligence (AI)-enabled 3D vision navigation technology for autonomous mobile robots (AMRs). Sevensense was founded in 2018 as a spin-off from Swiss technical University, ETH Zurich.
The acquisition follows ABB’s minority investment in Sevensense after it joined the company’s innovation ecosystem in 2021, the same year ABB acquired ASTI Mobile Robotics.
ABB will integrate Sevensense’s technology into the company’s AMR portfolio, offering speed, accuracy, and payload.
Sevensense’s navigation technology combines AI and 3D vision, enabling AMRs to make intelligent decisions, differentiating between fixed and mobile objects in dynamic environments. Once manually guided, mobile robots with Visual Simultaneous Localization and Mapping (Visual SLAM) technology create a map used to operate independently, reducing commissioning time from weeks to days and enabling the AMRs to navigate in highly complex, dynamic environments alongside people. Maps are constantly updated and shared across the fleet, offering instant scalability without interrupting operations and greater flexibility compared to other navigation technologies.
The technology can potentially impact robotics beyond AMRs, leading to greater efficiency, flexibility, and accuracy throughout production and intralogistics. The technology will also continue to be sold across material handling, cleaning, and other service robotics fields under the product name Sevensense.

Explore the March 2024 Issue
Check out more from this issue and find your next story to read.
Latest from Aerospace Manufacturing and Design
- NASA selects instruments for Artemis lunar terrain vehicle
- Twin-cutter boring head
- Bell awarded funding for X-plane build phase of SPRINT program
- Shaft coupling clamps
- #46 Lunch + Learn Podcast with SMW Autoblok
- Gleason Corp. acquires the Intra Group of Companies
- Thread milling cutter reduces cutting pressure, vibration
- Malaysia Aviation Group orders 20 more Airbus A330neo widebodies