

When machining difficult products, do we really use all the tools we have available? Obviously, part geometry dictates what we must do to produce parts needed, however, it doesn't dictate how we can create the shapes.
One area of concern for many shops and programmers is tool life when machining forgings or materials with a tough outer layer. While working with customers who deal with this problem, we observe how they process these parts. We should look at trying to process these parts in three distinctive phases.
1: How do we remove the tough outer scale areas? In many cases we see processes that simulate what I would classify as finish machining passes. In other words, using tooling that simulates the final geometry of the part and exposes the nose radius of the tool. This is the weakest area of the tool and using it this way generates heat, harming tool life.
Lead-angle tooling allows you to use the strongest edge or radius of the tool and reduce the heat being put back into the part. Many times, machinists dismiss lead-angle tools or even round tools because they do not match the finished part geometries. One common argument says lead-angle and round tools add time to the machining process. However, downtime due to poor tool life and broken tools often adds more process time than slowing down the machine to protect the tool.
2: Prepare the part of the finish pass. In this phase you may need to add a pass or a tool to generate corner radii or other geometries that will allow you to finish the part with the finish pass. For instance, if a milled surface calls for a square shoulder, you may have to add a tool that allows you to remove material left by the roughing tool that has a 45° lead angle.
3: Finish the part with the final geometry. This will require tooling that matches the finished part geometry and allows us to have a quality finished part for minimal cost.
In many instances, we review what the cycle time is to evaluate the total cost. However, total cost also includes the downtime to change tools, costs of broken tools, and the frustration that the operator endures to run the machine to produce these parts.
When we have difficult parts to produce due to hard material, we can use geometry to solve our manufacturing problems. Ask your tooling provider to help you select the proper geometry to produce your parts at the lowest possible cost.
Do you have specific topics you would like addressed or cutting tool challenges? Email me so I can address them in a future column: miker2468@aol.com
CMR Consultants
miker2468@aol.com
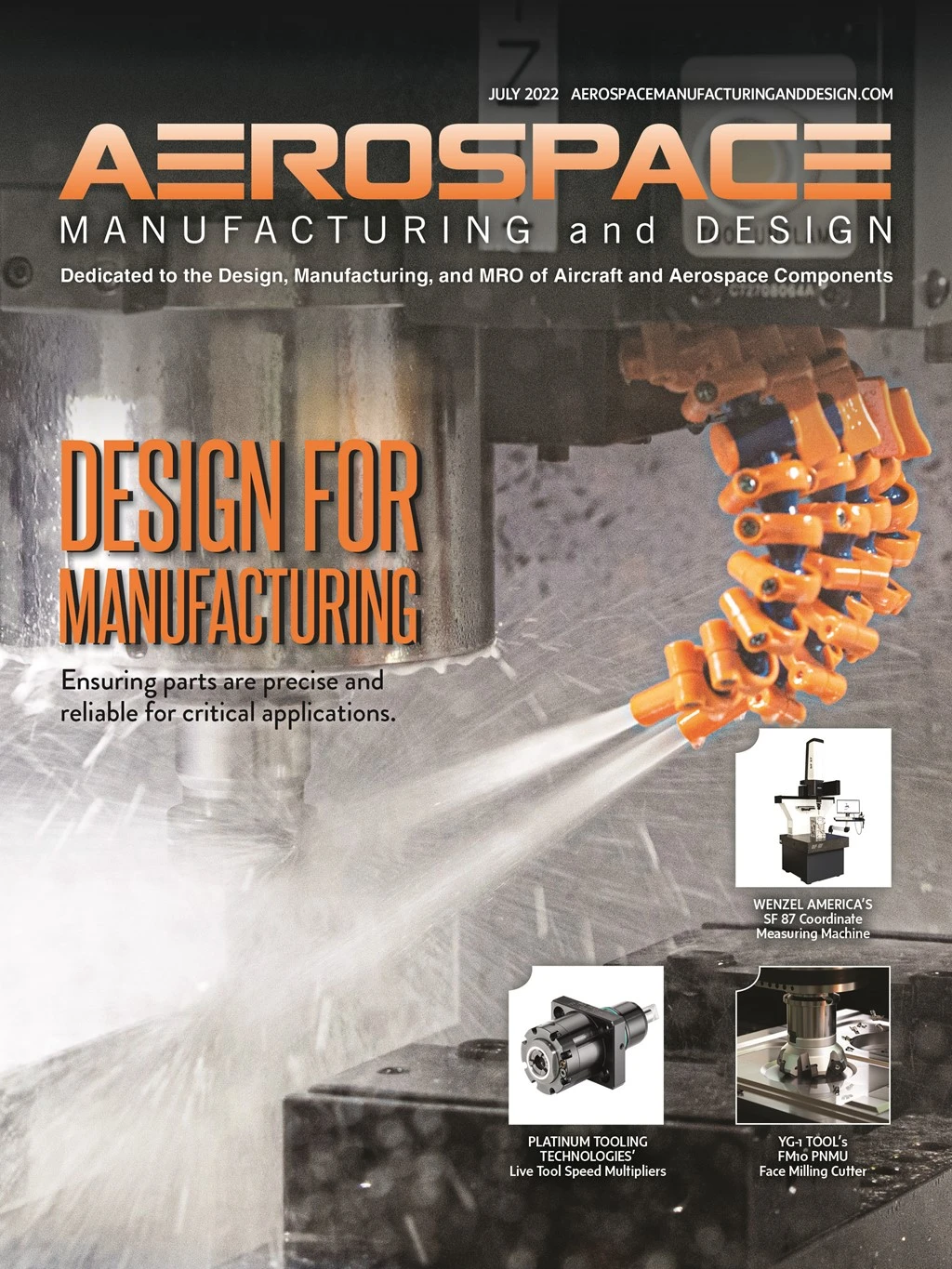
Explore the July 2022 Issue
Check out more from this issue and find your next story to read.
Latest from Aerospace Manufacturing and Design
- America Makes announces QTIME project call
- Innovation meets precision for 40% faster machining
- Upcoming webinar: Pro tips from a supply chain strategist
- Heart Aerospace relocates to Los Angeles
- Fixtureworks introduces Stablelock Clamps
- Piasecki acquires Kaman's KARGO UAV program
- PI Americas’ long-travel XY piezo nanopositioners-scanners
- AAMI project call submission deadline extended to May 12