
Multi-billion dollar programs from the world’s leading aerospace suppliers are regularly stung by failure to meet delivery dates, resulting in significant penalties. If machining engine components in emerging nickel-based alloys is one of the pain points, ceramic tooling in the right application can result in significant, 2x-to-5x performance increases.
Know when to air cool and when to use fluid coolant– Ceramics are having a large impact in roughing hard-to-machine superalloys such as Inconels and other nickel-based alloys, but their cutting performance can be tempered by being brittle compared to carbides. To maximize ceramics performance and life, the correct cooling application is crucial.
Proprietary nickel-based alloys used for turbine blades are among the world’s strongest materials, continually being developed to allow aircraft engines to run at much higher temperatures. Superalloys such as Inconel, Waspaloy, and Rene are useful for parts that require high strength, high-temperature creep resistance, phase stability, and resistance to oxidation and corrosion.
Rough machining these materials with ceramics requires some consideration. The machine tool has to provide enough horsepower, torque, and speed for high material-removal rates. The setup has to be rigid, and the ceramic tooling should maximize cutting performance. Ceramic inserts, such as the double-sided KCRA grades from Kennametal, are thinner than previous models and allow for cutter designs with higher pocket density and faster running times, particularly with nickel- and cobalt-based alloys. The round, flat-top geometry reduces the incidence of notching, and a secure clamping system makes changing inserts easier and more dependable.

Air coolant in the clamping system delivers air flow to the insert’s cutting edge, improving chip flow and insert life. Since the KCRA ceramic platform is meant to run dry with regular air or cold-air blast for chip evacuation, the reduction in coolant consumption can cut costs even more.
While milling with ceramics runs dry, turning with ceramics requires the right amount of coolant. Ceramics need heat to run well, so too much coolant in turning can be counter-productive. Establish a range based on your equipment, toolholder, and coolant delivery. High-pressure coolant systems of 1,000psi work well with catalog parameters in clearing chips and keeping the pocket clean. On some dedicated equipment, ultra-high pressure coolant will be applied at increased parameters.
Think system– Improving production efficiencies while machining hard alloys means maximizing metal-removal rates with low cutting speeds and significant cutting forces. Specialty milling and turning centers feature improved stiffness and damping on spindles and sizable machine structures to minimize undesirable vibrations that deteriorate part quality and tool life. Although these advances have added to greater productivity, the weakest point has often been the spindle connection.
The most critical parameters of a taper-face spindle connection are the clamping force and radial interference. Maximizing clamping force and selecting appropriate values of interference can further improve connection rigidity.
Using three-surface contact, KM4X engineering produces 3x the bending moment resistant capacity compared to other tool systems. This means:
- Shops can increase speeds and feeds in difficult machining applications, gaining productivity from the machine tool
- A smaller KM4X100 connection can equal or better the cutting performance of a larger connection
- KM4X systems can be applied on multi-tasking, turning, machining centers and transfer machines in manual, semiautomatic, or fully automatic mode
- KM4X can perform in operations from low-speed/high torque to high-speed/low torque, allowing manufacturers to get the most out of their equipment
– While ceramics have been on the metalworking scene for decades, modern grades are not your father’s tooling. For example, the KCRA platform also improves trochoidal milling strategies, which can aid in milling high temperature-resistant alloys. Conventional roughing involves multiple, straight-line passes through the material. Trochoidal milling uses a combination of periphery milling and circular interpolation in the X- and Y-planes. When done correctly, it minimizes changes in the chip load and achieves high and constant feed rates, most commonly employing a low radial depth of cut with high axial depth of cut. It can save significant time and money by achieving higher speeds and feeds while reducing loads at the cutting edge.
Kennametal Inc.
IMTS 2016 Booth #W-1522
About the author: Matthieu Guillon is global portfolio manager/advanced materials for Kennametal Inc. He can be reached at matthieu.guillon@kennametal.com.
Get curated news on YOUR industry.
Enter your email to receive our newsletters.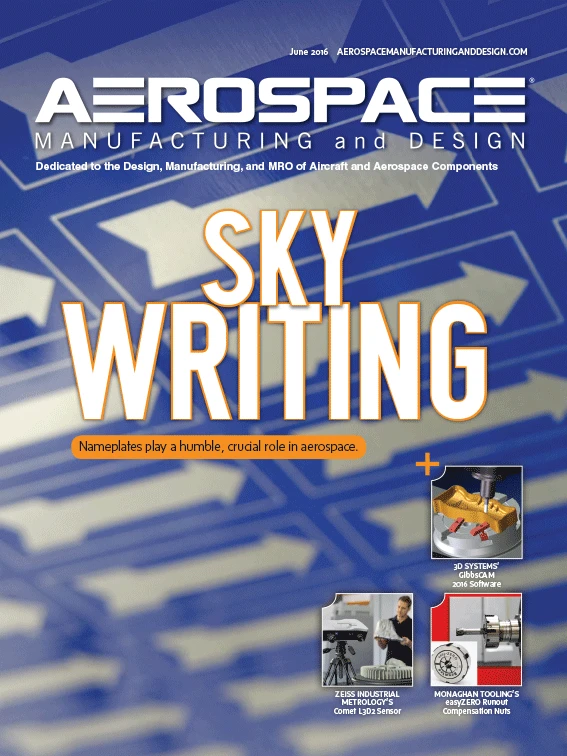
Explore the June 2016 Issue
Check out more from this issue and find your next story to read.
Latest from Aerospace Manufacturing and Design
- Revitalizing the Defense Maritime Industrial Base with Blue Forge Alliance
- Safran Defense & Space opens US defense HQ
- Two miniature absolute encoders join US Digital’s lineup
- Lockheed Martin completes Orion for Artemis II
- Cylinder CMMs for complex symmetrical workpieces
- University of Oklahoma research fuels UAS development
- Motorized vision measuring system
- Everyone's talking tariffs