
The aerospace industry continues to reduce its carbon footprint, investing in alternative fuels, more efficient airframes, and better engines. Combined with fuel-saving gains in operations and transformations in air transportation systems, an
For the plants that manufacture parts for those airframes and engines, however, the environmental situation is more concerning. According to ProComplianceWare – a developer of web-based solutions for industries to manage compliance obligations – many aerospace manufacturing companies do not have adequate processes in place to cost-effectively manage waste streams or environmental compliance. As a result, they are at risk for penalties and fines that can escalate into the millions of dollars.

Examples of environmental violations by aerospace industry manufacturers illustrate the scope of the problem and potential consequences:
- 2007 – A Connecticut manufacturer of aerospace systems pleaded guilty to two counts of violating the federal Clean Water Act by discharging wastewater contaminated with hexavalent chromium and copper into a nearby river in excess of the amount allowed by the company’s permit. The company agreed to be placed on probation for five years and pay a $1 million fine. Other penalties included contributions to environmental programs and facility upgrades with a potential price tag of $11 million.
- 2011 – A California metal plating company that does work for the aerospace industry was fined $100,000 for poor storage of toxic wastes and hazardous sludge, which the Environmental Protection Agency (EPA) determined was a potential danger to employees, the surrounding community, and the environment.
- 2017 – A Washington company that manufactures parts for the interiors of some types of aircraft was fined $38,000 by the state Department of Ecology for violations that included not handling waste correctly, failing to send hazardous waste to approved disposal sites, not handling spills properly, and not labeling hazardous waste containers appropriately.

These numbers, as well as the hundreds of waste streams that an aerospace manufacturing facility could potentially produce, are more than enough to keep everyone in a plant’s environmental health and safety department awake at night. For many environmental compliance managers and providers of waste reduction solutions, the biggest hurdle continues to be the battle for capital expenditure. Too often, managing waste and mitigating the associated risks is a secondary process to production. When a plant’s performance is primarily measured by output, it’s easy to see why capital budgets are so heavily tilted toward production equipment and processes.
3 steps
Environmental responsibility and sustainability are important to an aerospace manufacturer’s bottom line. Steep financial penalties associated with failing to comply with local, state, and federal waste regulations as well as ISO 14001 environmental management standards that mandate a reduction of a manufacturing facility’s waste streams, emissions, and carbon footprint create a huge risk for a company to avoid. That’s why it shouldn’t be an either/or decision between production equipment and waste management solutions. Both are critical to a plant’s ability to conduct business and be profitable.
Aerospace manufacturing facilities must take three steps to become environmentally responsible while maximizing profitability:


1) Initiate an environmental compliance policy.
Establishing an environmental sustainability protocol mitigates risk and protects a plant from potential fluid disposal liabilities. For example, chips and turnings saturated with free liquid can become a liability for the manufacturer if a lawsuit is filed against a recycler that disposes of hazardous materials improperly. Manufacturers can still be held liable for fines and penalties even though metal and coolant wastes have been removed from their site by a recycler.
The more used coolant or machine oil a manufacturer sends to the recycler, the greater the chance of being implicated if disposal problems arise. By proactively addressing fluid and chip remediation, manufacturers can shield themselves from liability merely by proving good intent. So, even without a formal environmental policy in place, the minimum requirement should be to map one out using ISO14001 as a baseline.
While ISO 14001 does not state specific requirements for environmental performance, it does provide a framework a company or organization can follow to set up an effective environmental management system. ISO 14001 can provide assurance to company management and employees – as well as regulators, customers, and the public – that environmental impact is being measured and improved, which in turn can reduce the cost of waste management as well as the consumption of energy and materials.

2) Identify areas in the plant where risks can be mitigated.
Aerospace manufacturers that do not adopt a formal environmental policy can still seek opportunities for material savings and environmental improvements that can be immediately realized. Grinding/honing operations, cleaning processes, and recycling practices related to wash and mop water should be on the list, but a company’s machining operation is an obvious place to begin an environmental, health, and safety assessment.
This is the point where scrap metal and coolant wastes are generated by equipment such as screw machines, gantry mills, CNC lathes, and drills. Reclaiming and recycling these materials improves workplace safety and reduces environmental impact. It can also bring a significant financial benefit to an operation, evident when you analyze the equipment options available.

3) Implement the latest technology and processes.
Volume reduction is the key to effectively managing solid waste material in aerospace applications. The current trend is to reduce the material at the front end of the processing system using a crusher or shredder unit at the discharge of the CNC conveyor. This process:
- Reduces the frequency of handling and transferring full hoppers
- Eliminates safety issues around the machine
- Prevents equipment damage caused by material and belt jamming
- Allows plants to get higher value for their scrap, because the recycler is hauling away a full 40,000 lb container, not a container filled mostly with air
Passing through a crusher or shredder system will also give the material a shovel-grade consistency for further processing through a wringer unit. A modern centrifuge or chip wringer will remove upward of 98% of the free liquids from the material.
Another modern trend in aerospace manufacturing is to use

A
- Highest reduction of scrap volume
- Recovery of waste oils, coolants
- Reduction in hazardous waste handling costs
- Higher recycled material price, as fines can also be
briquetted (especially true with aluminum) - Reclaim more than 95% of spent fluids by compressing, grinding swarf
- Dual compression systems are modular, for easy installation in any layout
After the cutting fluids have been reclaimed by wringing or compressing, consider implementing a coolant recycling or filtration system. Aerospace manufacturing plants should strive to eliminate the problems that occur when tramp oils and suspended solids are allowed to accumulate in
Properly designed filtered-coolant systems remove free-floating and mechanically dispersed tramp oils, fine particulate, and tool debris from individual sumps, central systems, and wash tanks. They also:
- Extend tool life
- Contribute to higher-quality part production
- Reduce costs associated with coolant purchases, maintenance
Other solutions include ultrafiltration systems, which extend the life of wash water, rinse water, floor scrubbing solutions, synthetic coolants, and pressure wash solutions by controlling the content of oil and solids. These systems are also used for disposal of waste coolants and oily waste waters to help meet zero manifesting goals and comply with local, state, and federal environmental regulations.
Conclusion

Environmental compliance is a continuous improvement process (CIP) whereby systems and equipment should be constantly evaluated and improved to achieve maximum efficiency and effectiveness, especially regarding overall environmental impact. Although they operate in an industry known for futuristic technological advances, many aerospace manufacturers are behind the curve with their waste management and recovery processes.
The task of implementing or updating a waste management system doesn’t have to be daunting. Several options can allow an aerospace manufacturing facility to incrementally improve its approach to dealing with waste streams, but the process must start somewhere. Working with an equipment and systems provider that can specify, supply, and support the latest waste management technologies can bring much-needed relief to environmental compliance managers who understand the necessity and business benefit of industrial waste recovery.
PRAB
www.prab.com
IMTS 2018 Booth #121124
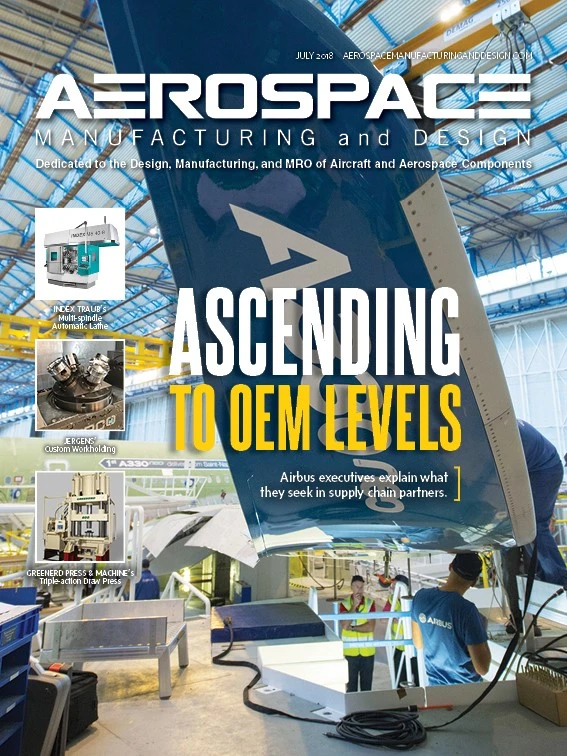
Explore the July 2018 Issue
Check out more from this issue and find your next story to read.
Latest from Aerospace Manufacturing and Design
- March Manufacturing Lunch + Learn with Quell Corp.
- March Manufacturing Lunch + Learn with SMW Autoblok
- SwRI addresses critical aging aircraft issue
- Walter adds tools to its PCD milling cutter range
- Archer Aviation, Palantir partner on next-gen aviation
- Fairlane Products’ TG GripSerts and accessories for low-profile clamping
- Boeing to build US Air Force’s sixth-generation fighter jet
- Sandvik Coromant introduces CoroMill Plura barrel