If you are looking for gear manufacturing equipment – such as gear cutting, forming and finishing, as well as broaching, shaping and slotting machines, you must visit the Gear Generation pavilion. In addition to traditional applications, gears are finding even greater importance in a large range of markets. » North Building |
Hobbing Large Diameter Gears
The H 400 is capable of running small lots or mass producing straight and helical gears; crowned and tapered gears; worm gears; chain sprockets and toothed belt discs; cluster gears; and special profiles. The H 400 can use standard hob or form milling technology, ranging from dry or wet machining, with high capacity HSS or carbide tools to skive hobbing of heat-treated gears.
Also on display will be single-flute gundrill machines, multiple diameter carbide drills and reamers, the Star PTG-6L tool and cutter grinder, and gear cutting tool solutions.
IMTS Booth N-6924
Star SU LLC
Hoffman Estates, IL
www.star-su.com
Turning Alternatives
Precision electro-chemical machining technology (PECM) presents a production process that opens up completely new fields of application. PECM is a process for the machining of high-alloyed materials, such as nickel- and titanium-based alloys. All electro-chemical machining processes are characterized by stress-free material removal, smooth transition points, and surfaces without ridge formations.
IMTS Booth N-6846
EMAG LLC
Farmington Hills, MI
www.emag.com
TableTop Tool Sharpening Machines
The TT6-36 tabletop and TT-SP6-24 tabletop special broaching machines are available in a 38" x 44" footprint. Featuring a 20" x 20" tabletop size, both machines move at a 5fpm to 30fpm. Both the TT6-36 and TT-SP6-24 are capable of broaching keyways, internal splines, and various other part forms. The CNC Automatic Broach Tool Sharpening Machine can sharpen helical or standard gullet, flat, or specially shaped broach tools up to 12" in diameter and 120" long.
IMTS Booth N-7027
American Broach & Machine Co.
Ypsilanti, MI
www.americanbroach.com
Sawing, Machining Center
The ACS + CFMcurve integrated sawing and machining center, features a proprietary sawing algorithm with a servo motor-controlled feed to continuously adjust critical sawing parameters during each cut. The CFMcurve machining center simultaneously machines each workpiece end using 12 independent servo-controlled axes. Machining options include: threading, boring, profile turning, grooving, radius edges, and angled chamfering. Bundles of mill length stock, up to 16.5m long, are placed in an automatic loader, individually separated, and fed to the sawing process.
IMTS Booth N-6737
Rattunde Corp.
Grand Rapids, MI
www.rattunde.com
Gear Hobbing Machines
Genesis models 210H hobbers accommodate gears up to 210mm in diameter, including those with shaft lengths up to 350mm. Features include: Siemens 840D controls, integrated chamfering and deburring, and a high-speed loading system to reduce load/unload cycles. Various cutting tools, including high-speed steel and carbide hobs, as well as a tool sharpening service are available.
IMTS Booth N-7000
Gleason Corp.
Rochester, NY
www.gleason.com
The KX 500 FLEX incorporates a direct-drive work spindle, tailstock support, and dressing spindles. The ZX 1000, the big brother of the KX 500 FLEX, shares common machine elements and software with the KX 500. The large ductile iron bed and torque motor for high-load capacity allows high-speed grinding of frac bull gears with a dressable worm tool.
IMTS Booth N-7036
Kapp Technologies
Boulder, CO
www.kapp-usa.com
Profile Grinding
Design of the Liebherr LFG series profile grinding machines are for profile grinding of external and internal gears. The series includes three models for workpiece diameters from 800mm to 1,250mm. The LFG 1000 is for workpieces up to 1,000mm diameter will be shown at IMTS. The direct-drive table with swivel axis allows high-production grinding of topologically-correct, or topologically-modified tooth profiles, single- or double-flanked. In the standard LFG model, dressing of the grinding disc is accomplished by a single dresser combined with the shift and swivel axis.
IMTS Booth N-6930
Liebherr Gear Technology Inc.
Saline, MI
www.liebherr-us.com
Get curated news on YOUR industry.
Enter your email to receive our newsletters.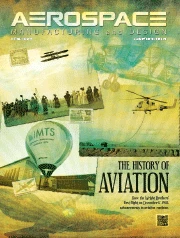
Explore the August September 2012 Issue
Check out more from this issue and find your next story to read.
Latest from Aerospace Manufacturing and Design
- Ralliant to establish global headquarters in North Carolina
- Philatron MIL-DTL-3432 military cables
- Beyond Aero refines its hydrogen-electric light jet
- Americase's advanced protective solutions
- Social media - what are your thoughts
- GE Aerospace secures Air Force engine contract
- Thomson Industries' online sizing and selection tool
- #53 - Manufacturing Matters - 2024 Leaders in Manufacturing Roundtable