![]() |
The use of advanced ceramics in the aerospace and defense industries continues to expand. Because the production of critical ceramic components requires a high degree of engineering expertise and manufacturing know-how, the collective abilities of engineers and manufacturers to define, specify, and produce the correct surface roughness for a particular application may determine whether the component will perform to specifications.
Advanced ceramic materials are unique because they are susceptible to subsurface damage during the machining process. Machining of the same component can be performed by two different companies, both meeting the same generic dimensional and surface finish specifications, yet one part fails in its application. This consideration is one of many issues related to surface roughness that aerospace and defense professionals should understand to ensure that a component is manufactured at a reasonable cost, delivered on-time, and has the ability to perform as designed. Various machining methods, such as diamond wheel grinding, lapping, and polishing greatly affect surface roughness. Metrology is also critical for verifying and confirming the results.
Typical uses of ceramics within the aerospace and defense industries include:
- Mirrors (lasers, telescopes)
- Radomes
- Gas turbine components (shrouds, vanes, blades, blisks)
- Transparent windows and domes
- Rocket components
- Nuclear components
Application Considerations
To understand how a component will be used in a given application, familiarity with strength and optical considerations is essential. Diamond wheel grinding is the primary way of machining advanced ceramic components to meet tight dimensional and surface roughness requirements. The diamond wheel grinding process itself creates subsurface damage that can directly affect component strength. Several parameters such as wheel grit, bond type, depth of cut, speed, and feedrate can influence the amount of subsurface damage created. Increased subsurface damage decreases the strength of the component, and directionality of the grind lines can affect component strength in high stress areas. It is important to realize that components are often designed using material strength values derived from the results of very specific ASTM standards. Machining of test specimens that meet ASTM standards requires using strict guidelines that dictate the wheel grit, speeds, and feed rates. Often, these parameters are not translated to the detailed drawings of the final component, leaving a delta between tested and actual material strength based on how the material was machined.
![]() BOTTOM: In contrast, the lapped finish has lines that are hard to resolve by visual inspection, and has no definite orientation. |
Surface Roughness is critical for optical applications with the main consideration being minimal subsurface damage. Optical components typically have very tight surface roughness specifications, often in the sub-nanometer Ra range, which require lapping and polishing with increasingly finer abrasives to eliminate the subsurface damage. Frequently, the same vendor does not perform all operations on a component, so it is critical to specify the correct surface roughness at each step to mitigate subsurface damage, manage costs, and decrease lead times.
There is a wide range of advanced technical ceramics, and each has unique properties regarding surface roughness. There are monolithic, infiltrated materials, composites, and porous materials. It is important to be knowledgeable about the potential for pullout, reaction layers, porosity, and substitution of “lower grade” materials because one’s choice of material can have a tremendous impact on surface roughness.
Along with material selection, cost is always an important factor. Unnecessary or vague surface roughness requirements can increase the cost and lead times significantly. Ongoing communication between the customer and precision fabricator is critical from project start through delivery. Such close interaction is useful in determining inspection methods upfront to ensure that parts conform to specifications. Frequent communication also helps both parties establish reasonable lead times so that delivery of components, even those with unique requirements, occurs on-time and on specification.
Manufacturing Considerations
Advanced ceramics are typically machined utilizing diamond wheel grinding, lapping, and polishing. Diamond wheel grinding consists of using a grinding wheel with industrial diamonds bonded to the periphery to remove ceramic material from the component thus achieving the desired dimensions and surface roughness. There are many types of grinding wheels such as resin-bonded, metal-bonded, vitrified, and electroplated. Grinding considerations, in addition to bond type, include abrasive size and concentration. Parameters of the grinding process such as depth of cut, orientation of grind lines, plunge vs. reciprocating, wheel truing/dressing, and spark outs can affect surface roughness. One must weigh all of these considerations when grinding to obtain the correct surface roughness while ensuring the part will function correctly in its application.
Lapping is the process of using a loose abrasive between two surfaces that rub together, thus abrading the part. This method is typically used to achieve a surface roughness and flatness beyond the capabilities of standard grinding. The difference between a ground part and a lapped one is clear. (See Figure 1 above) The type of abrasive and lap material is based on the type of material being lapped and is critical because the choices will affect material removal rates, surface roughness, and how well the lap holds its form. A softer lap allows more of the abrasive to embed in it and produce a better finish with less material removal. If the lap is harder, the abrasive will be free to roll and produce more removal, but the finish will not be as good. Along with the changing of laps, abrasive size decreases accordingly to yield better finishes.
Another way to increase removal rate is with machinery that can be automated, or that is designed specifically for accelerating the process with pneumatics and faster spinning speeds. Although the traditional method of hand lapping can produce highly accurate and repeatable results, it is a time-consuming process. Clearly, having a component lapped to a specified finish in a reasonable amount of time requires taking many variables into consideration.
Polishing is similar to lapping in concept, but the process of removing microscopic surface roughness (asperities) is complicated. Polishing can involve the removal of molecule clusters at an atomic level. Because polishing occurs at such a small scale, it is often difficult to explain effective ways to remove asperities. There are differing opinions on how, and why, polishing works with a majority of what we know coming from empirical data. Depending upon the component material and kind of abrasive used, mechanical and chemical removal mechanisms can work together or independently to achieve the desired result. Another polishing consideration is the kind of material used as the lap. A lap can range in hardness from cast iron or tin to wax or pitch.
Using zirconia toughened alumina (ZTA) substrates as examples, one ZTA piece is polished with an aluminum oxide (Al2O3), and another with a diamond abrasive, giving both surfaces a mirror finish. Nevertheless, a surface roughness profile shows that there are major differences between the two surfaces. (Figure 2)
The combination of a felt lap and a heterogeneous diamond slurry results in superior stock removal with a uniform finish as the abrasive affects the surface evenly and consistently. The felt lap and the Al2O3 will not remove the stock as rapidly, and will affect only the weaker parts of the surface, leaving behind traces of damage that can affect how the part will perform, especially in wear component applications.
Considering all of the variables involved in polishing, there are no simple rules about how and when to use it. The best way to meet a polishing requirement is relying on experienced hands who can prevent over-specifying and the resulting waste by calling for tolerances that are too tight or exceed limitations of the material being used.
Metrology Considerations
Metrology is critical for inspecting and quantifying a specific surface roughness when dealing with advanced technical ceramics. There are two basic ways of verifying a surface roughness: contact and non-contact. Both methods require technical expertise to understand when and how to use them.
The most basic method is a visual comparison to a known standard. While relatively crude, it can be useful when verifying a relatively coarse surface roughness in an area difficult to reach by other means. It does, however, open possibilities for error due to interpretation differences.
A Perthometer is a contact method of checking surface roughness for values greater than 2 micro-inch. It consists of a diamond-tipped stylus that measures surface variations based on vertical displacement of the stylus as a function of position. Various parameters that can affect measurements are the size of the radius on the stylus, traverse length, and what filters are set. Advantages of a Perthometer are that it is not sensitive to surface contamination, color of the material, or the reflectance of the material. They are often portable, allowing in-process inspection on the machine, a flexible and low-cost option. Precautions to keep in-mind are that the diamond-tipped stylus can wear quickly on ceramic materials and the stylus can scratch some parts. A stylus also has limitations on hard-to-reach geometries, and it does not work well on certain kinds of materials, such as porous ceramics. When using a stylus, the operator should ensure that measurements are taken “across the grain” to ensure the maximum roughness value is obtained. (Figure 3)
White Light Interferometry is a non-contact, optical method used when specifications require accuracy unachievable with a Perthometer. The optical profiler collects data over a field of view instead of a line, negating grinding orientation. Additionally, there is no risk of surface damage, and data gathered may be filtered or transported to software for interpretation. The optical profiler also allows for surface examination from different perspectives and can make measurements in the sub-nanometer range (<0.04 micro-inch Ra). Drawbacks include the inability to measure work in-process on the machine and surfaces with low reflectivity. It also collects data over a relatively small area, which may not be representative of the entire surface. Furthermore, ceramic microstructures can cause discontinuities that require filtering.
Regardless of which inspection method is used, the manufacturer and customer need to agree upfront about performing measurements identically on comparable instruments. Failure to do so can result in correlation issues that may affect part acceptance.
Conclusion
Typically, most detailed drawings lack the specifications required for producing and inspecting a successful ceramic component. Therefore, open communication is critical. Ongoing interaction among individuals who understand the application and those who produce the part is critical to the success of the final component. Additionally, effective lapping, polishing, grinding, and metrology require a combination of experienced engineering and manufacturing professionals with outstanding judgment and state-of-the-art equipment. Working closely with a knowledgeable machining company that understands how machining can affect final component performance is key to the success of any given application.
PremaTech Advanced Ceramics
Worcester, MA
prematechac.com
Get curated news on YOUR industry.
Enter your email to receive our newsletters.
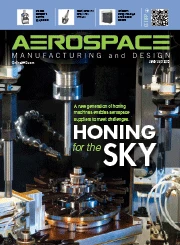
Explore the June July 2012 Issue
Check out more from this issue and find your next story to read.
Latest from Aerospace Manufacturing and Design
- March Manufacturing Lunch + Learn with Quell Corp.
- March Manufacturing Lunch + Learn with SMW Autoblok
- SwRI addresses critical aging aircraft issue
- Walter adds tools to its PCD milling cutter range
- Archer Aviation, Palantir partner on next-gen aviation
- Fairlane Products’ TG GripSerts and accessories for low-profile clamping
- Boeing to build US Air Force’s sixth-generation fighter jet
- Sandvik Coromant introduces CoroMill Plura barrel